Innovation From the Ground Up
Water and energy savings innovations earned Fontanini Foods the Green Plant of the Year award.
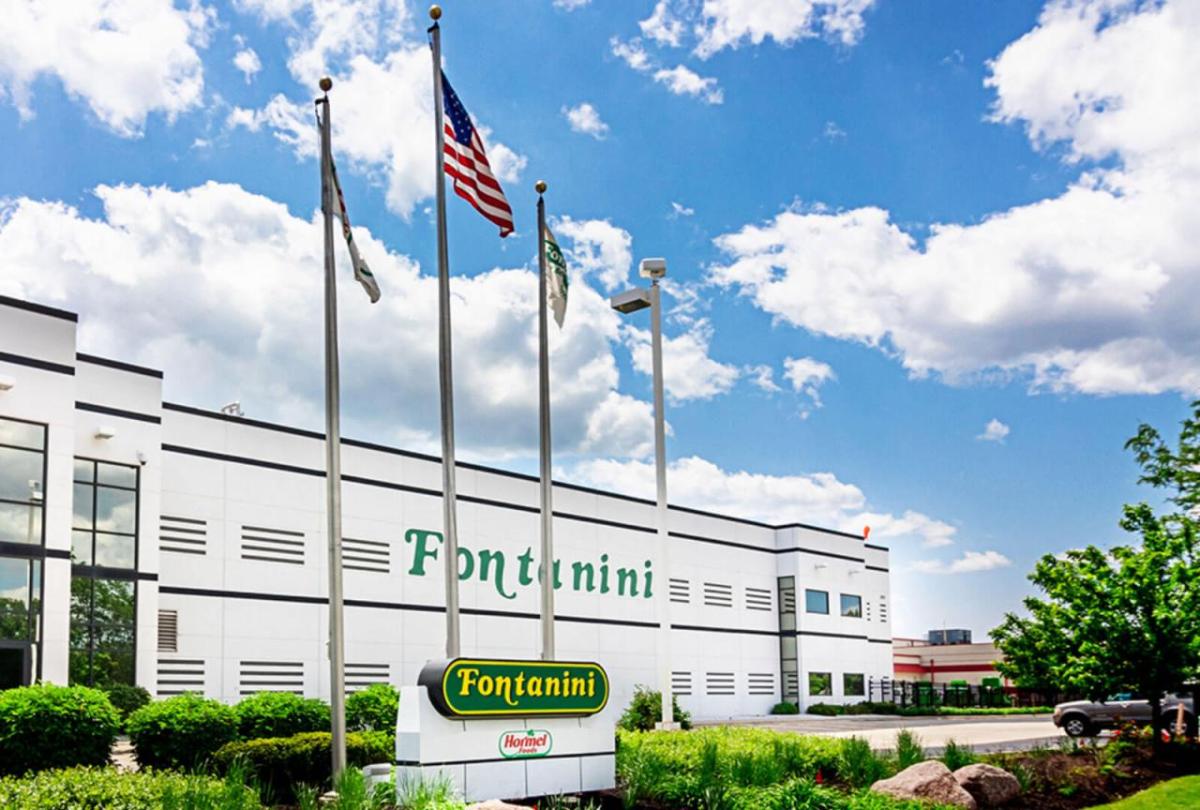
Talk about a win-win-win.
A Hormel Foods plant just outside Chicago that makes premium Italian meatballs, sausages and pizza toppings has found a way to save water, reduce energy use and transform byproducts into biodiesel.
The company’s Fontanini Foods plant in McCook, Ill., has 60-foot-long ovens that “use a lot of cooling water to prevent overheating,” said Michael Wysocki, the plant’s engineering manager. The water also evenly distributes the heat load.
Until a couple of years ago, when this water got too hot (about 180 degrees), it would go down the drain. “So we found an opportunity to install some water recovery tanks, pumps and controls, and we’re reusing this water,” Wysocki said. “We capture it.”
According to Wysocki, the hot water is pumped to two large boilers that supply steam for the plant’s processes. This saves water and captures “free heat” so the boilers don’t need to use as much natural gas to turn water into steam. The modifications were so groundbreaking, “the oven manufacturer had never heard of it before,” Wysocki said. “We thought that was pretty cool.”
Innovation Leads to Award
Hormel Foods purchased the Fontanini plant from its family founders in 2017. The inventive strategies to save energy and water led Fontanini Foods to garner the 2023 Green Plant of the Year award from Food Processing magazine. Hormel Foods is the first two-time winner of this prestigious award.
Andrew Sieren, Fontanini plant manager, said that from their first day on the job, team members are encouraged to “look for waste in the process” and search for opportunities to reduce it. “It’s in our DNA.”
The Hormel Foods Sustainability Best of the Best competition, held each year, recognizes team members’ best practices. “It’s highly competitive,” Sieren said. “And teams enjoy bringing forth what they’re working on. It gets the competitive juices flowing, and it is a big deal at the plant to win that award.”
Among the innovations that earned the Fontanini facility Green Plant of the Year is a reverse osmosis system that removes impurities, such as calcium and magnesium, from the plant’s water supply.
“Just like that stuff can clog up your coffeemaker at home, it does the same thing in plant equipment,” Wysocki said. “As you use more water, you have to find a way to eliminate that buildup.”
According to Wysocki, this elimination is done by “forcibly blowing down water to flush that stuff out of the system every once in a while. What the reverse osmosis system does is remove a lot of those impurities, so you don’t have to do this blowdown as often, which is essentially wasted water.”
TURNING
Byproducts into Biofuel
The Fontanini plant also uses a skimmer to harvest used cooking oil and other food manufacturing byproducts from ovens and water cookers, and in partnership with a rendering company, DAR PRO Solutions, turns that waste into biodiesel.
“There’s a compounding sustainability side to it, creating green energy,” Wysocki said. The lessons of these water- and energy-saving innovations can spread far and wide through the Hormel Foods best-practice initiative, where advances made at one plant can be shared with engineers at the company’s other facilities.
“We had our plant engineer conference here in April where we had our entire engineering group, from corporate, the plants, everybody all together,” Wysocki said. “We had good discussions about all the different things that not only we’re doing, but other cool innovations around sustainability that a lot of the plants are doing.”
DUBUQUE FACILITY
Reduces Water Use
Wysocki cited the Progressive Processing facility in Dubuque, Iowa, another facility owned by Hormel Foods: “They’re doing a lot of cool stuff, some of it revolving around a reverse osmosis system,” he said. That system has reduced water use by more than 7.2 million gallons, a 9% reduction in water use plus an 11.6% reduction in wastewater at the plant where bacon bits, Hormel® Compleats® meals and SPAM® products are made.
7.2m gallons of water saved
11.6% reduction in wastewater at another Hormel Foods plant
Through best-practice sharing, Wysocki said, “even if it’s not necessarily identical equipment or an identical process, we try to help work through the same major concepts and give each other ideas and brainstorm.” The goal is to “think about ways that you can apply what you’ve learned in one place and use that to the maximum benefit anywhere.”
Wysocki notes that the Hormel Foods 20 By 30 Challenge, which includes climate leadership and waste reduction goals, has served as a catalyst for team members in all sectors of the company to offer solutions and strategies.
TEAM MEMBERS TURN
Experience into Innovation
“Some of our best ideas, some of our biggest breakthroughs, really do come from engagement with our plant professionals and with our mechanics, people working on sanitation, quality control, really anywhere in the plant,” Wysocki said. “Those are the people with the best understanding of the day-to-day process. They’ve seen a lot; they do a lot. And they really have some of the best ideas.”
Wysocki added that these innovations are “not so much a top-down driven exercise, although corporate sets out the challenge.”
It really helps drive that engagement, it also enables team members to see that they’re making a big impact.
MICHAEL WYSOCKI, ENGINEERING MANAGER AT FONTANINI FOODS
Citing an example, he says an oven operator, “one of our second-shift team leaders led a focus group on figuring out how to recover a lot of the oil that is generated inside these ovens, some of that grease and stuff that cooks off the product. Historically, we had to separate it out using expensive equipment and chemicals in our wastewater pretreatment operation before it would eventually get discharged to our local water district.”
Wysocki’s team “really dug deep and came up with some pretty cool ways” to recover more oil. “Working with my team we were able to modify some pumps and controls and give them the tools that they need,” he said. “Then our vendor would haul some of this material away and give us some credits for it.”
A BOOST FOR MORALE
And the Bottom Line
Saving energy and being better environmental stewards is a morale boost for team members, Wysocki said. Through a reporting structure devised by the industrial engineering group, workers can see what’s working and what could be improved.
“It really helps drive that engagement,” Wysocki said. It also enables team members to see that they’re making a big impact.
Energy conservation has become more important in recent years as fuel costs have risen, Wysocki added. “Food plants inherently have a lot of utility demand,” especially when you have to have a refrigerated facility. “So we have a unique opportunity to make a big impact on utility costs by being able to innovate and share ideas. If you can reduce those costs, that has a huge impact on the bottom line.”
Even relatively minor changes, Sieren notes, such as replacing lighting in the facility with LED bulbs, can make a significant difference, financially and for the environment.
“But there’s always more we can look at,” he said. “There’s a lot of good things going on, but a lot of more good things to come.”