8 Steps to Fleet Electrification
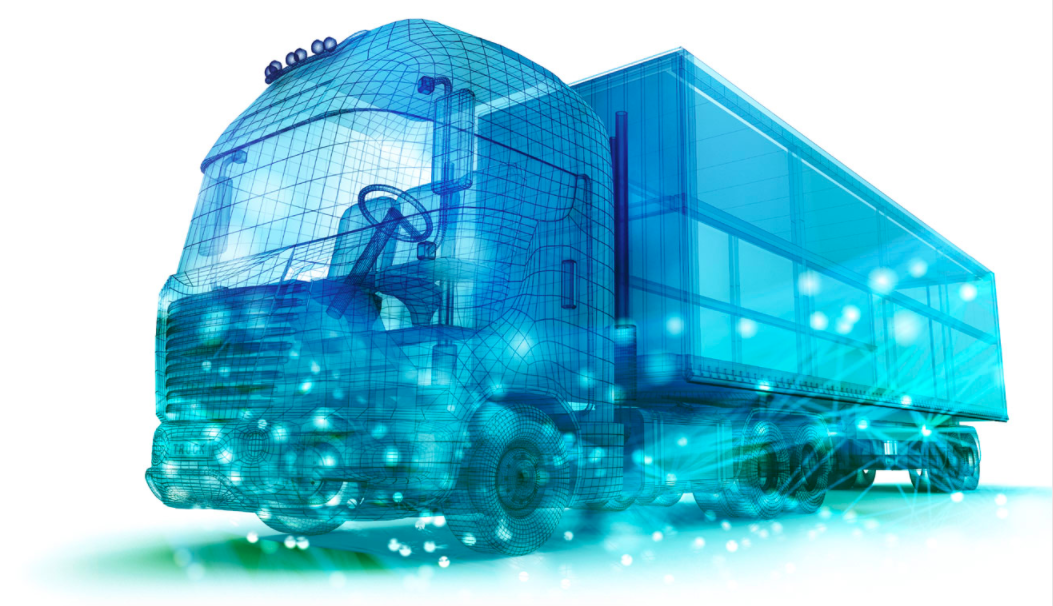
Transportation in the U.S. is rapidly becoming more sustainable, competitive and innovative. Encouraged by new advances in electric trucks, vans and buses, fleet and sustainability managers are turning away from the combustion engine, lured by the promise of zero emissions, cost savings on maintenance and fuel, and improved driver safety.
These benefits, paired with the decreasing cost of battery storage and improved battery performance, are driving the electrification of medium- and heavy-duty vehicles.
But to make this new electrified world a reality, fleet and sustainability managers must navigate a new maze of technologies, infrastructure choices and supply chains. As if that wasn’t intimidating enough, they must also consider power and telecommunications infrastructure as a critical part of their operations.
Why Go Electric?
Coast to coast, fleet and sustainability managers are looking at pilot programs and launching fleets of electrified vehicles. Doing so will achieve several critical measures:
Achieve strict emissions standards.
According to Bloomberg, the U.S. e-commerce and delivery sector consumes 5.4 million gallons of diesel per day, which the Greenhouse Gas Equivalencies Calculator equates to outputting 55,000 metric tons of carbon emissions. To address this, regulators are passing stringent regulations on fuel economy and emissions, driving transit agencies, school districts and e-commerce and delivery companies like Amazon, FedEx and UPS to deploy cleaner, quieter fleets.
Lower operating and maintenance costs.
The fuel economy of electric fleets is far better than their diesel counterparts – the Environmental and Energy Study Institute states that electric buses get 5x more fuel economy than diesel buses operating on the same route. When looking at the total cost of ownership, one electric school bus is $31,000 cheaper than diesel, and one electric transit bus is $81,000 cheaper, according to WISPIRG. Plus, advancements in vehicle-to-grid (V2G) capabilities will help enable peak shaving, demand charge management and revenue streams as two-way power flow and utility digitization advances – the Clinton Global Initiative finds that pilot programs show that one V2G eBus can generate $6,100 annually.
Improve safety and working conditions.
Electric drivetrains are quiet and fumeless, and without a loud, vibrating engine to distract the driver, can provide several safety and operational benefits. By improving the driver experience and reducing driver fatigue, eFleets can help improve driver retention. In addition, on-board telematics can monitor and collect speed data, enabling managers to encourage safe driving habits.
The Eight Steps
To help make this process as smooth, seamless and cost-effective as possible, Black & Veatch has designed an eight-step framework to help fleet and sustainability managers develop their charging infrastructure strategies.
Step 1. Define Fleet and Operational Needs
Defining fleet requirements will determine capacity and operational needs. How many electric vehicles do they plan to employ? What will be their duty cycles and routes? When and where will the vehicles charge? Charging options vary widely, and can include depot charging, on-route, shared and endpoint charging, or a combination. Managers must confirm this information up front to develop an infrastructure plan that meets current – and future – capacity needs.
Step 2. Review and Select Technologies
Managers can then move on to selecting the types of medium- and heavy-duty vehicles for their fleet. This will also determine the scope of the charging network – e.g. the charging connectors, charging speeds and networking capabilities – necessary to meet demand. Once the hardware is in place, managers can then consider the software and network solutions that will help manage charging and costs and integrate on-site facilities and distributed energy resources (DERs).
Step 3. Analyze Charging Load and Power Demand
Heavy and mid-sized commercial fleets rely on Level 2 and DC Fast Charging technologies that require enormous amounts of energy. For example, a fleet of 56 electric buses uses around 11 MWh/day while a fleet of 542 buses could demand 109 MWh/day. Managers must analyze their energy demands before considering which technologies will provide clean, resilient and secure on-site power generation and energy storage.
Step 4. Implement Site Design and Planning
Adding high-powered charging load will require work to upgrade the equipment and building facilities. Most existing charging facilities will be retrofitted, which will require careful consideration of layout, physical space and power supply. To add new sites, managers should implement an informed site selection process to help control schedule and cost.
Step 5. Coordinate with Utility Partners
Managers must engage with their utility partners as early as possible during the design process. Managers, technology integrators and utilities must work together to develop power delivery roadmaps that integrate utility programs and charging rates, and calculate savings based on future charging loads. Stakeholders should plan for long-term power capacity, looking ahead at least five to 10 years, and anticipate future infrastructure needs.
Step 6. Apply for Permit and Approvals
The larger the facilities, the more complex the right-of-way, permissions and permitting requirements. Plus, the fact that many of these new products and technologies are still in flux may make it even more challenging to get permits approved. Other required paperwork can include state environmental impact filings, interagency agreements and approvals, and equipment paperwork. Many states are working to expedite these processes.
Step 7. Distribution Grid Upgrades
The addition of high-powered charging load and DERs will require upgrades to the distribution grid, or even new equipment such as utility feeders and substations. Substantial upgrades will drive up cost and schedule. On average, a power delivery schedule without grid upgrades is about an eight-month process, while a schedule with grid upgrades (such as installing a new substation serviced by new transmission lines) can last 48 months or more.
Step 8. Obtain Equipment, Construct and Commission
Once all the approvals and permits are in place, site construction can begin. The construction process will be far-ranging, involving exterior work (e.g., boring, trenching and paving) and internal work (e.g., drywall, painting and ceiling repair), and require some type of storage to protect the equipment during installation. Once full power has been delivered, commissioning and testing can begin.
Learn More
Electrification of medium and heavy-duty vehicles is advancing fast, spurred by lower operating costs, improved driver safety and the promise of a lower-carbon future. These eight steps are designed to provide a framework that will help fleet and sustainability managers as they work to develop charging infrastructure strategies.
Well-informed planning is critical to allow for scalable growth and total cost efficiency. To learn more, enjoy the Black & Veatch and CALSTART webinar, Alternative Energy Solutions for Fleet Electrification & Resiliency and download our free eBook, Electric Fleets: Eight Steps to Medium- and Heavy-Duty Fleet Electrification.
You may also enjoy this complementary article, The Mandate For Companies Looking To Electrify Fleets: Start Planning Now.