Automotive Application Corner: On-Board Charging (OBC) for Electric Vehicles
by John Grabowski
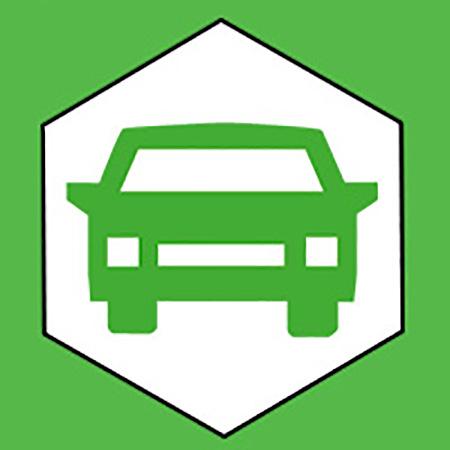
Read this story on the ON Semiconductor Blog
Battery electric vehicles (BEV) and plug-in hybrid electric vehicles (PHEV) have high-voltage battery systems used for propelling the vehicle. These battery systems require a means of charging them when not in operation. The most common systems use 300V-400V batteries, although some manufacturers are beginning to specify 800V battery systems as a means of improving vehicle efficiency. Regardless of the battery voltage or type, they need a method for daily charging.
One method is through the use of a fixed charger, which can be installed in a garage or at public sites. However, the need may arise to charge the vehicle in a remote location which does not have a dedicated charging source. In this event, a charger must be available on-board the vehicle that can use typical AC mains voltage and connections. This requirement forms the basis of the need for an on-board charger.
The OBCs of today take on many different designs, while always balancing their power level versus the cost and weight. The vehicle manufacturer must define the appropriate on-board charging power level based on overall vehicle requirements. Chargers come in many different power levels and the higher the power level, the shorter the charging time. These chargers require significant power from the AC mains and are powered from either single or three-phase sources depending on the design of the on-board charger.
Four common power levels have evolved, determined by typical AC mains power availability around the globe. The 3.3kW and 6.6kW chargers have become the basic building blocks for all power levels of chargers. Both 11kW and 22kW chargers are realized by combining three of the single-phase units, each running from one of the three phases.
The majority of on-board chargers are designed using a typical set of building blocks for the construction of the single phase chargers.
The AC input source is filtered, rectified and fed to a multi-phase PFC circuit. The PFC circuit is a switching circuit which is responsible for controlling the periods of conduction, with respect to the input sinewave, for aligning the input current drawn with the input voltage. This voltage-current alignment creates a high power factor on the AC mains and is required through regulation by most utility companies. This process is broken into several phases to spread the conduction loss over a wider group of components. The next block uses an H-bridge converter to chop up the DC voltage and deliver it to the input of the transformer. This block is typically designed with a resonant LLC circuit and the control of the magnitude of the applied voltage to the transformer facilities the regulation of the power applied to the battery. Finally, the output of the transformer is rectified, filtered and connected to the high-voltage battery.
With the rapid increase of BEVs and PHEVs in the market, it is likely that the design and construction of OBCs will be a common requirement for years to come. Learn more about our vehicle electrification solutions today and how our design resources can assist you in reaching higher efficiency and reliability.