Building a Culture of Safety: A Transformative Approach to Environmental, Health and Safety
Environmental, Health and Safety (EHS) is more than just saying the right things and ticking the right boxes. And determining how safe a project is shouldn’t just be measured by its incident report or lack thereof.
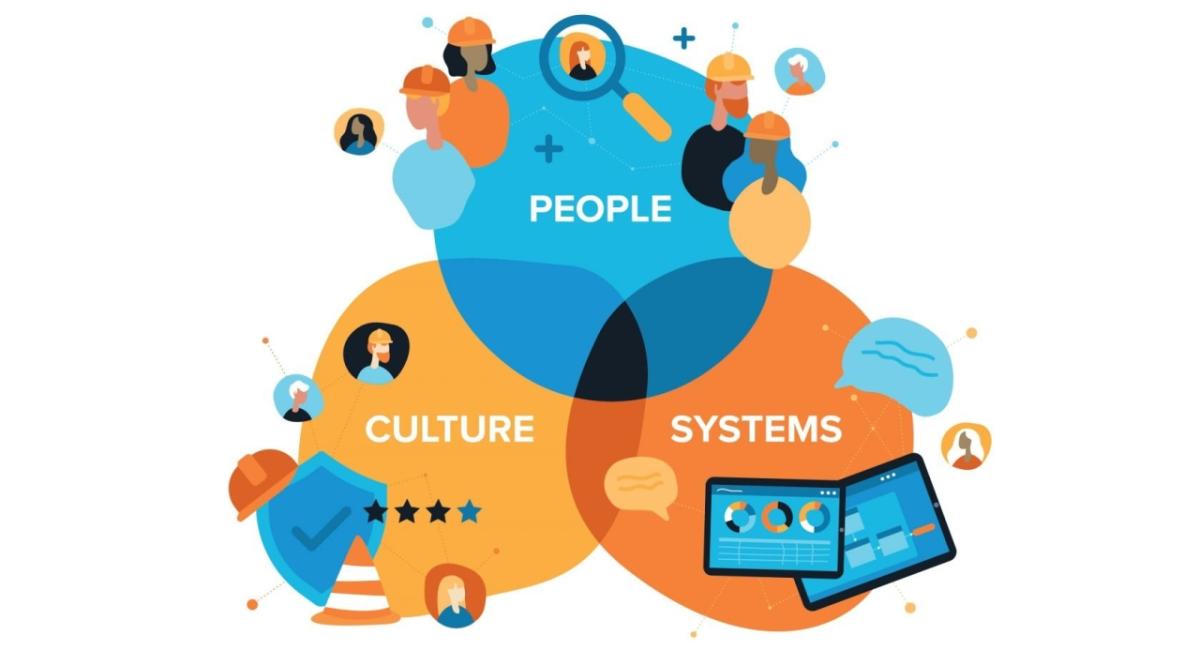
While metrics are important, this way of thinking leaves little room for proactivity and preemptive action. It incentivizes teams to score well in the almighty audit and results in performative and superficial safety solutions. When we are preoccupied with tedious bureaucracy, and motivated primarily by avoiding penalties, we lose sight of what is the single most important reason for EHS practices: making sure everyone gets home safe to their loved ones.
Right now, the highly competitive landscape and inflated operations costs have put increased pressure on construction companies to do more with less time and money. It’s imperative that this pressure does not contribute to cutting corners that have a real impact on employees’ well-being.
With intention and collaboration, it is possible to build a culture of safety by designing an intelligent and robust EHS strategy that doesn’t endanger your budgets or timelines.
So, what makes for an effective EHS strategy? In our opinion, the following are three must-have elements that work together for safer sites:
- People: identifying, hiring, and retaining the ones that can demonstrate alignment with the organization’s culture.
- Systems: avoiding mountains of paperwork while still making them comprehensive, easy, and enjoyable to use.
- Culture: establishing the health and safety of the team is paramount and non-negotiable— the only acceptable commitment is an organization free of incidents and injuries.
People: leading with values to find, and keep, the right talent
When it comes to EHS, building the right team is half the battle. A safe work environment takes buy-in from all levels of the organization and requires good communication between them. This begs the question: what makes a strong candidate for a role in EHS? How do you identify them and best utilize their talents?
Conduct value-led interviews
Of course, track records and metrics are an important part of interviewing, but they’re not the whole picture. Understanding a candidate’s core values will give you an idea of how well-aligned they are with your organization, and how well they can contribute to the culture you promote. Here are some qualities to look out for in an interview:
Are they passionate about working within a team?
When the candidate speaks fondly about their past roles, how do they describe their interactions with others? Do they strike you as a good communicator?
Do they view their team’s well-being as a motivator or a liability?
This one is a little harder to nail down but talking to a potential hire about past teams can be telling. Do they express that they see the value of people on their teams solely in terms of their output? Do they speak about hearing out the concerns of past teammates? Was it with an air of appreciation and curiosity or dismissiveness and irritation? Do they demonstrate an understanding of the value of solid relationships with both leadership and field teams?
Are they humble and enthusiastic about continued learning?
It’s counterintuitive, but an excellent sign of a candidate’s values is that they are self-aware and forthcoming about the gaps in their knowledge, and what they’re doing to learn more. Do they seem like they would be open to learning from someone lateral or subordinate to them within the organization? This will tell you a lot about their approachability and adaptability.
Recruit and reward internal talent
There are numerous benefits of nurturing and promoting within your organization, especially where EHS is concerned. It lightens the load of onboarding new candidates, conserving resources and time, and it also helps to bolster continuity in your organization’s cultural efforts.
Finally, recognition through promotion can do a world of good for the morale of existing employees. While working in EHS is good and rewarding work, it can also be high stakes and high stress, making it a less appealing field to enter. Conversely, when high-performing employees are going above and beyond, but see the company overspending on splashy hires, it can be detrimental to their morale, and the morale of their teammates and colleagues. Recruiting and rewarding internal talent addresses both of those issues.
Build a team of diverse thinkers
Occupational health and safety in construction is an inarguably specialized field and knowledge set. That said, it serves your organization to remain open to candidates with transferable skill sets from diverse backgrounds.
Successful leaders in this field need to possess a savviness for process, documentation, and regulatory framework. At the same time, they also require a solid level of people skills, especially in communication and conflict resolution. In this respect, candidates in medical and helping professions can offer tremendous insight and experience. Nurses, for example, have extremely stringent codes of ethics and procedural decision-making to adhere to, all while managing a demanding caseload with passion and empathy.
The goal of hiring equity is to make leadership more diverse and representative of the workforce. People with diverse backgrounds and experiences may catch potential hazards where others with a more “conventional” career trajectory may not.
For example, a major safety issue facing women in the workforce is improperly fitting personal protective equipment (PPE). Too-big goggles, bulky gloves and a lack of maternity PPE for expectant mothers are all instances uniquely affecting women that can lead to the improper wearing, or foregoing, of PPE. Already under-represented, women in the workforce may be reluctant to raise concerns with a safety manager. But having more women in leadership positions mitigates problems like this, makes workplaces safer for women and attracts more women to the industry.
Ultimately, EHS endeavors to embed practices that demonstrate the care we have for our fellow teammates into our day-to-day work. While technical knowledge and experience are great assets, soft skills and diverse thinking are just as valuable to your EHS strategy. These elements have a significant role to play in creating a culture of safety and are much harder to teach.
Systems: making it easy to do the right thing
It is tremendously difficult for even the most passionate staff or well-meaning culture to outweigh the impact of clunky and user-hostile systems. There is a delicate balance to strike with documentation and processes; they need to be simple and rigid enough to be easily remembered and applied, yet still flexible and dynamic enough to function in the reality of a construction site without suffocating the team’s workflow.
Holistic contractor evaluations
Aligning with contract partners that value EHS helps ensure buy-in from all levels. When you’re establishing your pre-qualification requirements, it’s essential to include the hard facts: incident rates, PHSA citations, fatalities, and training programs in place. Equally important is a measure of the team’s approach. Is their leadership engaged? Are they visible out in the field? Is there a clear, no-risk route for their employees to take with safety concerns? If not, can you really take the contractor’s self-reported qualities at face value?
Emphasize learning over penalty
Think about the traditional safety audit program: white helmets go out to sites and dissect them for what’s going wrong, score them against a checklist, and are never seen again. The data collected is widely circulated without context, publicly shaming the team being audited. This sends some harmful messages to the people working on site.
First, it enforces that the primary function of EHS is to placate leadership and that unsafe elements should be temporarily hidden away until the scrutiny is over. It implies that unsafe practices, as long as they are not captured on a checklist, are not important. Input from the people actually working in the space, in this scenario, does not add value and isn’t considered.
When we rethink the objectives and values of EHS measures, a better status quo emerges. A fear of penalty transforms into meaningful accountability, where people are given real autonomy in their own workspace.
At CRB we take a learning approach because we are confident that this yields a more accurate picture of the strengths and areas for improvement on each site. We are transitioning to a self-assessment mentality and offer real guidance on collecting information that is technical, systematic, and cultural. In doing so, we set up a more positive relationship, one of collaborators with a common goal. We take that data and formulate a comprehensive and impactful report with actionable items that both the site team and the organization can improve from.
Last, we believe that the audit must also identify flaws in the organizational process and identify how the bigger organization can better support the individual projects. How is the organizational leadership, through their behaviors, inhibiting or promoting a positive, sustainable culture of safety on the site? This is essential in continuing to grow and develop the effectiveness of EHS systems.
Use metrics for material change
Much as we advocate for collecting more robust and qualitative information on site, it’s imperative that the people taking the time to provide this intel can see their feedback being tangibly applied. This seems obvious, but too often well-intentioned surveys and data end up collecting dust or dying in the recommendations section of a report. This is not a good use of resources; it hinders transparency and it’s harmful to the morale of people on site. A sure-fire way to get people to stop taking EHS reporting seriously is demonstrating to them that their concerns are not being managed and that their time is not being valued.
User-friendly procedure learning and reference materials
Literally and figuratively, bulky learning materials are the enemy of continued learning. It’s not realistic to expect managers to lug around a hard copy on-site in hopes that they’ll refer to it when necessary; it’s also a major imposition on their time to navigate through such a document.
CRB is implementing Nintex Promapps® software, offering a flowchart of every Best Practice and Operations manual. With a step-by-step interface, users can easily walk through the whole process. This makes the information more digestible and easier to reference. Plus, having a digital version means you can take one single iPad on the road in place of heavy-duty three-ring binders.
Transforming all our EHS systems and processes to the digital Hammertech EHS software platform helps us review and support project teams virtually and in a non-threatening manner. Needless to say, it also streamlines the enormous documentation requirements that are part of any well-established environmental, health and safety program.
Collaborative EHS planning
To get the whole picture of how a site will run safely, it’s important to avoid siloed thinking when developing site-specific EHS plans.
Firstly, the entire project team must be engaged in developing the site-specific EHS plans. For example, our shift to a collaborative, information-gathering approach includes CRB leadership, clients, and our contract partners as stakeholders in the plans’ development. It recognizes that the people most able to assess the safety of the work are the people doing the work. Not only does this level of ownership help team members feel valued, but it also involves them as active contributors to site safety, further promoting a culture of safety. This can help EHS become a conscious and decisive part of their day-to-day, not just an afterthought to check a box.
In the case of supervisors leading the daily effort to develop Safe Work Plans, it is also imperative they engage their teams in this work. Too often the Safe Work Plan is developed without the input of the team executing it, and then the field teams are told how to complete the work safely. This sends the message that their input, knowledge and skill are not valued or trusted.
Instead, we’ve found that a better approach tells them what needs to be accomplished and engages the workforce in determining how they intend to do this work safely without anyone getting hurt. This opens a completely new level of engagement from our field teams, elevating the level of ownership and commitment to accomplishing the work safely. Through a simple shift to asking (rather than telling) our teams how to accomplish something in the field, we learn more about what they do and don’t understand and what risks they foresee before ground is broken. We also gain valuable insight into the mental state of individuals on the team— anticipating the personal work distractions that can lead to errors and injuries.
What’s the goal?
When we collaborate across levels and disciplines, the goal is to not only make the most of everyone’s insight and experience but also to send a clear message to our field teams: your value is in your unique knowledge and experience, not just your output.
Streamline onboarding
Even the biggest safety nerd will struggle to power through an all-day training. Consider where you can build in opportunities to get people on their feet and talking, taking breaks from passive and sedentary listening. Remember, most people don’t get into trades because they have a particular desire or aptitude for sitting around all day.
One easy way to take the load off your training days is to deliver site-specific training in a team walkthrough. The site manager tours the team around the environment, taking questions and clarifying expectations with practical and visible examples. This 45-minute walkabout offers an opportunity to stretch legs, build relationships and start off on the right foot with a new team.
At CRB, one of the critical intentions of any onboarding effort must be to have the new employees clearly understand expectations and also immediately feel like they are an essential part of the project or organization. When team members feel connected and valued early on, then they quickly begin impacting the success.
Culture: making safety your default
Leveraging your people and systems to support an EHS strategy is all well and good—as long as what is said matches what is done. Your workplace culture, in other words, is the guiding force that makes sure people do the right thing even when it is time-consuming and unpopular. Malcolm Gladwell proposes in The Tipping Point that when we pay attention to the seemingly smaller, less significant hazards, we can make better decisions to avoid putting ourselves at risk. These smaller examples set the tone and expectations of behavior on a project.
These expectations regarding how we work together and keep each other safe are critical and must be very clear. Team members need to know that doing the right thing is non-negotiable and shortcuts aren’t an option. When we talk about expectations, they need to include behavioral norms like stopping to ask questions if you don’t understand something. Similarly, if someone stops you from an unsafe act, you’re expected to respond respectfully, understanding they are looking after you and your family. Finally, if you see something unsafe you must intervene and will be supported in doing so.
Team members may be apprehensive to speak up when their intervention can cause increased costs and delays, so it’s important to outline accountability from an EHS perspective for them. Clarifying and abiding by these expectations is imperative in building a trusting environment where your team feels safe to do the right thing.
Safety by Design
When construction and design are separate entities, safety tends to be pushed out and only considered once boots are on the ground. However, we can take a more holistic approach that considers safety during the design process and achieves better outcomes. Safety by Design promotes collaboration between design and construction teams to ensure that projects are both safe to build and safe to use. For example, oftentimes there are design and engineering solutions that can contribute not only to the safety of those who will work, maintain and operate the facility, but also to the people who are working towards its construction.
By creating a culture of safety around a project that includes the design team, we prevent incidents, improve efficiencies, and deliver better projects. But how do you get design and construction working together from the very start? An integrated project delivery approach, like our ONEsolution™ process, creates early cross-team collaboration that enables safety processes and unified culture from the beginning. This is critical and impactful as the culture of the project team gets established before any contractors start working. For us, ONEsolution allows us to pre-empt safety concerns in the design phase so that construction crews aren’t working against the design they’re handed.
Build safe budgets
Resources need to be explicitly set aside for continued EHS support, training, and monitoring. This is not the budget line item to negotiate with the client, and if there is client pushback, you can make the case that a robust EHS strategy saves time and costs by pre-empting and avoiding shutdowns and injuries. Approaching this as non-negotiable helps your team to work with clients aligned to your values regarding employee welfare.
Treat people like people
An aspect of worker well-being that we don’t often talk about in EHS is mental health, but it can be just as important as physical safety. The impact of going to work every day in an environment where you are unsafe and unheard is demoralizing and dehumanizing. And as addiction and mental health issues are on the rise in our industry, making employees feel valued needs to be more than just lip service.
We need to view care and concern as opportunities and essential elements in establishing a safety culture based on dignity and respect for everyone working on the project. This will positively impact every aspect of the project far beyond the traditional safety measures. When people feel the leadership on the project and in their organization care for them and their families, they will take care of the business in turn.
Build in opportunities for continuing education
You don’t master a skill by taking one lesson once a year, so why would this work for learning and internalizing EHS? Instead, it’s much more effective to work engaging training moments into your day-to-day operations, which can also be easy and even fun. For example, at CRB we participate in a virtual company-wide Safety Moment, where employees of all levels volunteer to share an anecdotal example of safety in action in their personal lives with the team. This helps build a culture of curiosity and openness around EHS that leads to better attitudes and better outcomes.
Integrating a culture of safety at every touchpoint
When it comes to the safety, well-being, and livelihoods of our teammates, we know deep down that there is no convenience or savings that justify carelessness. But EHS can fall by the wayside in the bigger picture where it is balanced against budgets, schedules, and many channels of communication. That’s why it’s imperative to engage all aspects of your business, the people, systems and culture to view EHS as an asset and ultimately, to build a culture of safety. When our sites are safer, everybody wins.
The culture influencing safety on a project is fluid, constantly changing, and if it doesn’t get leadership’s attention, it deteriorates. That’s why safety must be promoted at the highest levels, and also the practices and processes that influence culture must be woven into everything we do. This means the project chartering process must include not only the business aspects of a successful project, but also the well-being of everyone on the project. We must make a concerted effort to build trust throughout the team with actions that demonstrate that care for our people is a core value. At the end of the day, we want everyone who touches the project to make it home safely, and not just by sheer luck, but because the project leadership led with integrity and cared for their team’s well-being, enabling everyone to contribute to a culture of safety.