Cummins Announces New Engine Design to Better Enable Low-Carbon Fuels
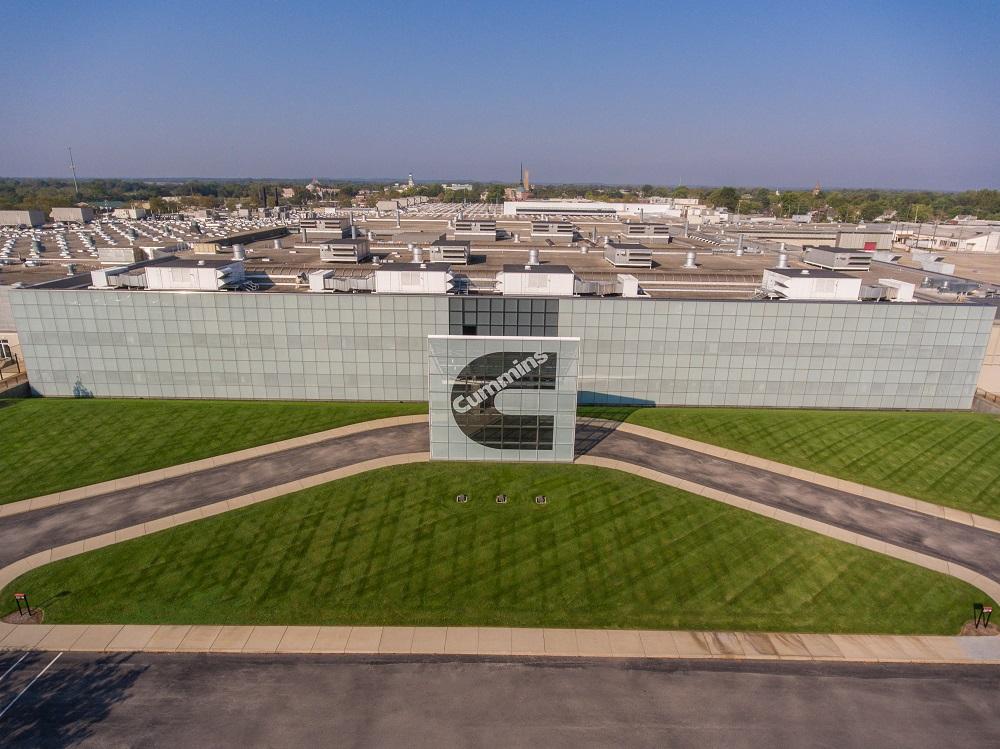
Global power leader Cummins Inc. is developing the industry’s first unified, fuel-agnostic engines, using engine blocks and core components sharing common architectures that can be optimized for different low-carbon fuel types.
These new fuel-agnostic engine platforms will have a high degree of parts commonality. Below the head gasket, each engine will largely have similar components. Above the head gasket, the engines will have different components for different fuel types. Each engine will operate using a different, single fuel, enabling customers to choose the best option for their particular circumstances.
“Getting to zero is not a light-switch event,” said Srikanth Padmanabhan, president of Cummins Engine business segment. “Carbon emissions that we put into the atmosphere today will have a lasting impact. This means anything we can do to start reducing the carbon footprint today is a win for the planet.”
Some customers may be ready for the low-carbon electrified platforms that Cummins has brought to market. Others, however, may not be positioned for that option and can reduce carbon by using advanced diesel, natural gas or hydrogen fueled internal combustion engines.
“We need to take action now,” Padmanabhan said. “Having a variety of lower carbon options is particularly important considering the variation in duty cycles and operating environments across the many markets we serve. There is no single solution or ‘magic bullet’ that will work for all application types or all end users.”
This new design approach will be applied across the company’s popular B, L and X-Series engine portfolios, which will be available for diesel, natural gas and hydrogen. Parts commonality will offer increased benefits for both truck original equipment manufacturers (OEMs) and end users, including similar engine footprints, diagnoses and service intervals. This means it will be easier for OEMs to integrate a variety of fuel types across the same truck chassis and there will be minimal costs to train technicians and re-tool service locations, resulting in a lower total cost of ownership for the end user.
“This is a new way of designing and developing lower emission internal combustion powertrains that meet the unique needs of the transportation industry while leveraging the benefits of a common product architecture and footprint where possible,” said Jonathon White, Vice President of Engineering, Engine business. “This unique technology approach will allow end users to more seamlessly pick the right powertrain for their application with the lowest CO2 impact.”
The powertrain decision can be extremely complicated, with issues ranging from access to certain fuels, cost and infrastructure to the carbon produced to power the grid in a customer's particular area.
The fuel agnostic engines are an important element of Cummins’ strategy to go further, faster to reduce the greenhouse gas (GHG) and air quality impacts of its products and reach net-zero emissions by 2050 in a way that sustainably serves all of the company’s stakeholders.
Two of the company’s environmental sustainability goals for 2030 goals include reducing scope 3 absolute lifetime greenhouse gas (GHG) emissions from newly sold products by 25% and partnering with customers to reduce scope 3 GHG emissions from products in the field by 55 million metric tons.
“Cummins is innovating at every level of the company to find new ways of working that use fewer of the world’s resources and the Engine business is at the center of this exciting innovation,” Padmanabhan said. “We know that our planet cannot wait for the perfect solution to happen.”