Cummins Celebrates Remanufacturing's Role in Sustainability
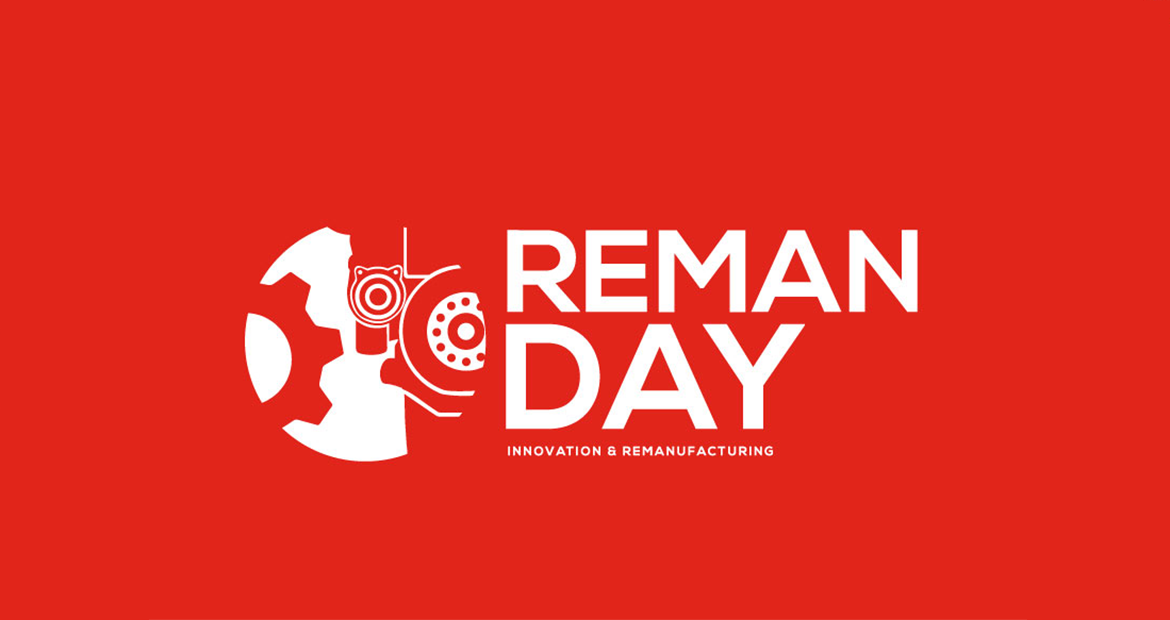
Global Power Leader Cummins celebrated 50 years of remanufacturing experience on Global Remanufacturing Day April 8, highlighting the important role returning parts to a useful life plays in the company’s sustainability efforts.
Up to 85% of an engine can be remanufactured and Cummins engines are built to be remanufactured multiple times. It also takes 85% less energy to produce a remanufactured engine, avoiding millions of pounds of greenhouse gases. An estimated 70 million pounds of material is reclaimed annually.
“Every day we give new life to Cummins products and keep them running for our customers,” said Rob Enright, Cummins General Manager of Cummins’ New and ReCon® Parts. “It’s just one of the many ways we drive dependability at Cummins.”
Cummins has implemented new tools and processes to improve its remanufacturing work over the years, including 3D printing , collaborative robots, laser cleaning and more. These innovations maximize remanufacturing efficiency while creating a safer workplace.
Remanufacturing will play a key role in Cummins’ PLANET 2050 sustainability strategy. The strategy includes specific goals timed to 2030 and the aspiration to be carbon neutral by 2050. One of the 2030 goals is to create a circular lifecycle plan for every part to use less, use better, and use again. The lifecycle plan for parts considers the reduction of remanufacturing waste, designing high value components to have sufficient life for multiple use cycles, and planning for material recycling – all of which are top initiatives within global remanufacturing.
Cummins is a proud member of Remanufacturing Day's sponsoring organization, the Remanufacturing Industries Council. The council is a strategic alliance of businesses and academic institutions that works across industry sectors to support the entire remanufacturing industry through a combination of collaboration, education, advocacy and research.