Cummins Plant Begins Building Prototype of Fuel Agnostic Engines To Prepare for Production
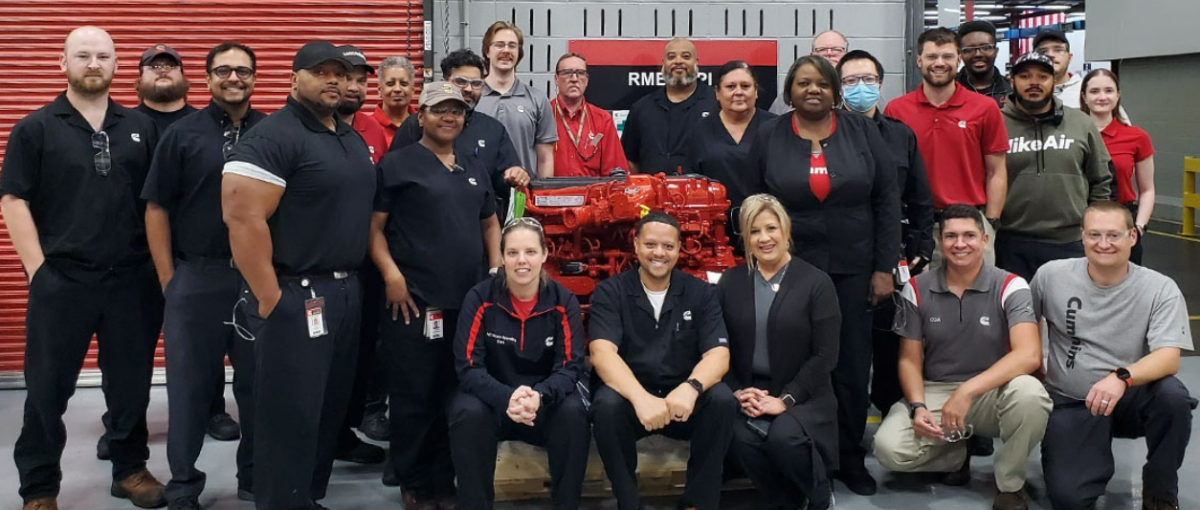
After building its 5 millionth engine, Cummins Inc.’s Rocky Mount Engine Plant (RMEP) in North Carolina is continuing its long history of innovation in engine technology and manufacturing. The next stop? Building fuel-agnostic engines in its VPI Lab.
VPI, or value package introduction, is the Cummins’ process for commercializing technology for the market through the definition, design, development and introduction of products, services and information for customers.
In 2022, Cummins unveiled the company’s industry-first fuel-agnostic internal combustion powertrain solution. The fuel-agnostic engine platform can be optimized for different low-carbon fuel types using a high degree of parts commonality to help reduce carbon emissions in commercial transportation.
RMEP’s VPI Lab will begin building prototype engines before they’re approved to hit the main assembly line. Various projects are in progress at the plant to upgrade the current production line and create a new low-volume production line, both of which will be capable of building both current and new Cummins’ products.
Plant personnel made upgrades to the VPI Lab to replicate the production environment for building the prototype engines. Run by two engineers, seven technicians and supported by a large cross-functional team, the lab uses prototype parts and replicates the manufacturing process of the assembly line to build the engines. This allows the team to identify errors, issues or roadblocks, ultimately decreasing downtime when the engine eventually moves to production.
Lab specialists validate the designs from a form, fit and function perspective. They make improvements as needed. It’s critical to spot any needed changes during the VPI phase, as it’s far more difficult to change the design and order of operations on the assembly line after the new engine goes into production.
“There’s a lot of work that goes into preparing our RMEP to manufacture a new product here,” said Chief Engineer Crystal Gwynn. “The VPI team works hard to identify any issues and get them resolved before full production manufacturing begins.”
Building the prototype engines at the same site where they’re manufactured opens up opportunities for collaboration between teams at the plant. Employees in the lab can train colleagues on new products and gain input to make each engine better.
“We want to build it first,” Howell says. “Since the engine will be manufactured here as well, we want to build it first, too. We know what we’re looking for, and we know how the engine is assembled. We want to refine that inside the plant.”