Cummins’ Progress in Reducing Emissions From Facilities and Operations
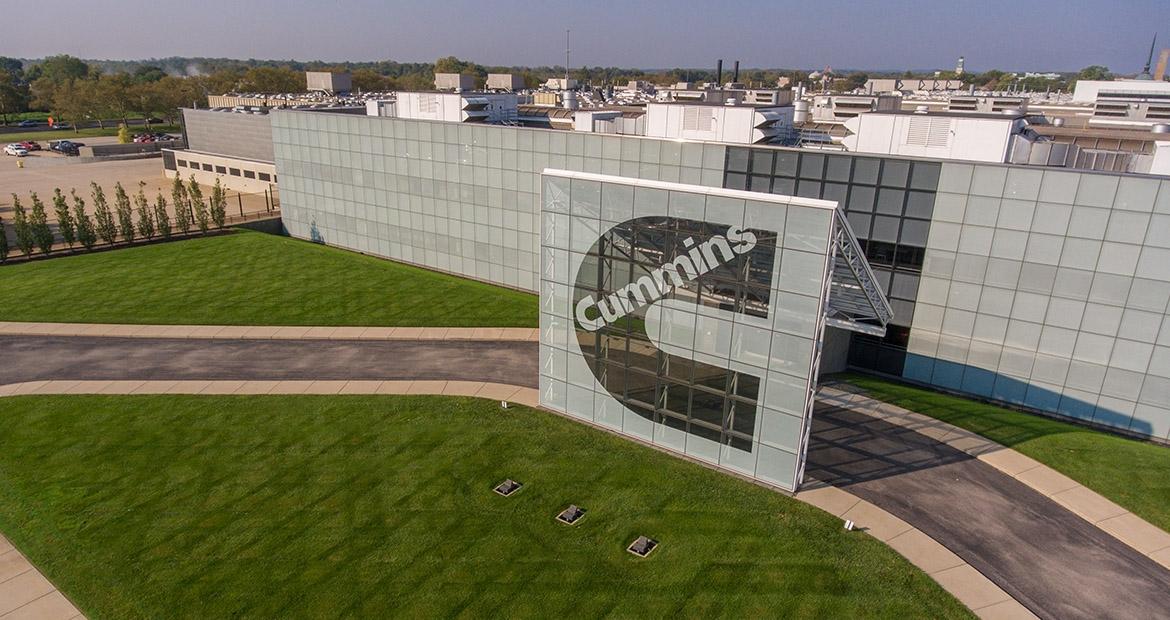
Cummins Inc. has a long history of setting ambitious sustainability goals and leading our industry in those efforts. We have worked diligently to align business and sustainability strategies to achieve the company’s mission of making people’s lives better by powering a more prosperous world. Our work impacts our customers, the communities we serve and the planet. It’s our ongoing mission to find new and better ways to power the world.
In 2019, we launched the PLANET 2050 environmental sustainability strategy, which includes nine environmental goals timed to 2030 and additional aspirational targets timed to 2050. One of the 2030 goals is a commitment to reduce absolute greenhouse gas (GHG) emissions from facilities and operations by 50%.
Our progress in reducing emissions from facilities and operations
In 2023, Cummins achieved an absolute total GHG reduction of 31% compared to baseline year 2018. This reduction amount is equivalent to eliminating 313,000 metric tons of carbon dioxide equivalent (CO2e).
Excluding recent acquisitions and organic business growth, GHG reductions from our facilities and operations show an absolute reduction of 33.5% from the 2018 baseline -- and we see significant opportunities for improved energy efficiency across our newest locations. Our efforts to improve facilities’ efficiency and sustainability are ongoing, and we continue making progress towards our goals. Here are some projects implementations from 2023.
In all, we invested over $18.8 million across 267 greenhouse gas reduction projects, which are estimated to save over 29,951 metric tons of carbon dioxide equivalent (CO2e) annually. That is equal to taking roughly 6,500 cars off the road[1].
Charleston Turbo Plant upgrades equipment to reduce emissions
In 2023, Cummins’ Charleston Turbo Plant reduced emissions by making a small, but significant, change to its equipment. By replacing obsolete turret lathes (large machines used to shape metal components for turbochargers) with upgraded equipment, the plant realized operational gains in addition to energy efficiency and water use improvements. These new machines also required less downtime and were more reliable.
Upgrades at the Columbus Engine Plant: VFDs and new hydraulic doors
Recent upgrades have also improved efficiency at Cummins’ Columbus Engine Plant (CEP). CEP is home to manufacturing and research and development for many Cummins products, including battery packs and electric driveline components and heavy-duty machining of heads and blocks for the X15 engine.
The addition of variable frequency drives
CEP installed variable frequency drivers (VFDs) which resulted in increased energy efficiency in process coolant. VFDs adjust motor speeds in real-time, reducing unnecessary energy use by matching motor output to demand. Compared to fan cycling methods, these VFDs can reduce energy consumption by up to 87.5%. The total annual reduction is estimated to result in almost 400,000 kwh per year.
Installing VFDs also optimizes operations and minimizes wear for process pumps and compressors, improving system reliability and longevity and cutting energy costs.
Switching from pneumatic doors to hydraulic doors
Another seemingly minor change that had major benefits for energy efficiency was CEP’s door control system upgrade.
Pneumatic automatic sliding doors, commonly used since the 1960s, are less efficient than hydraulic doors. Hydraulic doors offer better control, allowing facilities managers to control opening and closing mechanisms more precisely and reducing wear and tear. This upgrade improved safety, reduced downtime, and requires less labor and maintenance. Overall, we are moving away from the need for compressed air systems at facilities and exploring alternatives where there may not be a current viable option.
2023 achievements at a glance
From doors to cooling components to manufacturing equipment, we looked at our operations and found ways to improve operationally and environmentally.
In 2023, we completed 24 onsite solar projects to increase renewable energy usage, reducing roughly 14,486 metric tons of CO2e annually. Additional energy efficiency projects completed such as LED lighting and heating, ventilation and air conditioning upgrades and building envelope improvements are estimated to save over 5,433 metric tons of CO2e annually. Finally, we completed 55 manufacturing and compressed air system improvement products, leading to an additional 6,162 metric tons of CO2e annual reduction from our operations.
[1]https://www.epa.gov/energy/greenhouse-gas-equivalencies-calculator