Domtar's Plymouth Mill Continues Its Sustainability Journey
Domtar's mill in Plymouth, North Carolina, proves the adage that sustainability is journey, not a destination.
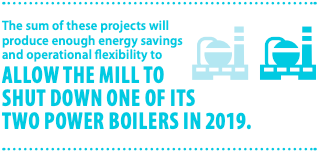
The Plymouth Mill, which got its start making pulp and paper in 1937, faced a bleak future as paper consumption declined precipitously in the aftermath of the Great Recession. But Domtar’s entry into the growing personal care market, combined with Plymouth’s access to the right fiber resources, gave the mill a new lease on life
After an investment of $87 million to repurpose the assets, in 2010 Plymouth became the first mill in Domtar’s manufacturing network to produce fluff pulp. Through the dedication and skill of its employees, Plymouth forged a reputation for quality and reliability in global markets, paving the way for an even larger conversion to fluff pulp at Domtar’s mill in Ashdown, Arkansas, in 2016.
As years went by, it became evident that the Plymouth Mill needed to further optimize its manufacturing processes and assets to remain viable in a competitive market. The smaller of its two fluff pulp machines was permanently shut down in 2018, and the mill embarked on a multi-year investment program, beginning with several energy and environmental sustainability initiatives.
The overall objective is to reduce the mill’s total energy footprint and thereby lower its costs, resource use, and environmental footprint. Capital projects at Plymouth in 2018 and 2019 included:
- Reducing steam use through several energy efficiency projects in the pulp manufacturing process.
- Reducing fuel use by improving the efficiency of one of the mill’s power boilers.
- Reducing fuel use to make steam by installing a condensing cooling tower and heat exchanger that will eliminate the use of about 11 million gallons per day of single-pass non-contact cooling water and recover heat from the process.
- Installing a thermal oxidizer to provide a back-up air emission control device when the power boiler is not available to incinerate gases produced in the chemical pulp manufacturing process.
- Reducing particulate matter emissions from one of the mill’s power boilers by installing a new electrostatic precipitator.
The Roanoke River ecosystem was also a major beneficiary of the project. Eliminating our need to intake “once-through” cooling water for the mill has removed the possibility of unintentionally entrapping and entraining aquatic life, including juvenile fish and larvae via that intake.
Domtar’s major investments in Plymouth are testimony to its commitment to the mill’s future and ongoing support for its sustainability journey.