Ecolab’s Safety Commitment
Working to ensure the safety of our employees, contractors, customers and communities
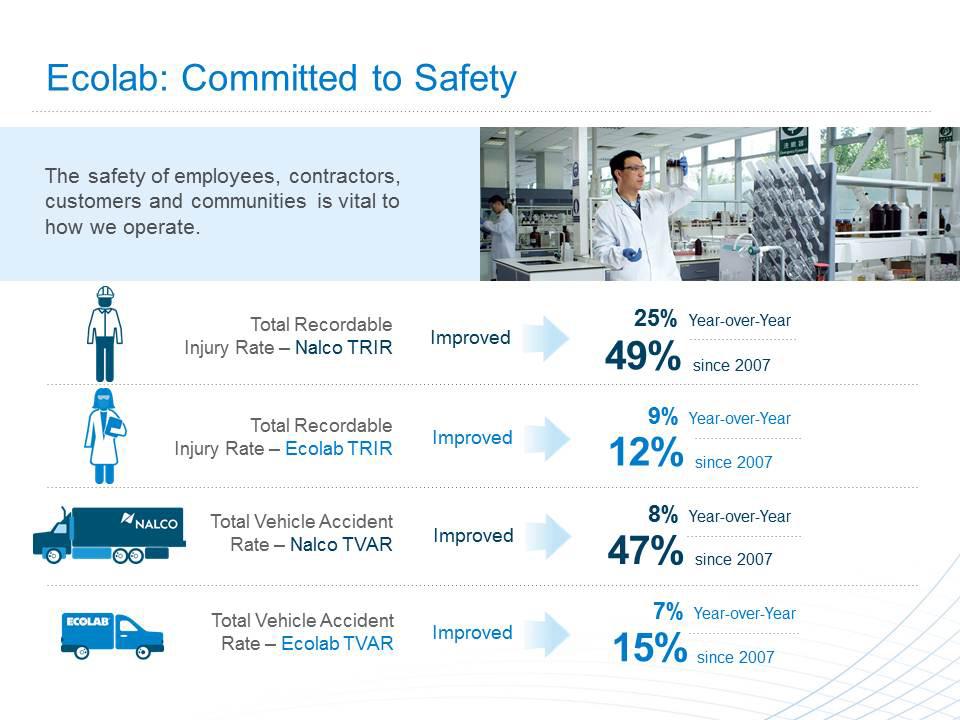
Safety is a critical part of how we work and is gaining renewed focus as we combine Ecolab and Nalco systems, processes and programs to shape our new safety culture. This effort provides the opportunity to take the best from each to ensure constant progress toward our goals of zero — zero accidents, injuries, fatalities and releases.
Globally we are deploying these best practices across three dimensions: Cultural, Structural and Quantitative. Culturally, we want to make safety a personal value for all employees.
Our “Reaching Hearts and Minds” communications campaign encourages employees to be accountable for their own safety and for the safety of those around them, 24 hours a day, seven days a week, 365 days a year.
We are driving structural best practices to manage risk and improve results. For example, we’re expanding Ecolab’s Compliance Assessment Process (ECAP) to improve safety, health and environmental compliance and reduce risk within manufacturing, sales, R&D and logistics. One of the greatest risks we face daily is driving. Our use of onboard monitoring devices provides drivers with immediate feedback that improves their behavior and encourages safe driving habits. Other best practices include fostering employee well-being through industrial hygiene, surveillance monitoring and ergonomic programs.
Leaders are accountable for the actions of those they supervise and we seek to create an atmosphere that not only makes it acceptable to identify and point out unsafe practices, but essential. We have instituted a Safety Leadership training course to integrate safety into leadership at all levels of the organization.
We track recordable injuries and vehicle accidents even though they are lagging indicators because it is important to quantify our performance. We are even more focused on leading indicators — activities that drive or help us predict future performance. These are critical in helping us cultivate a proactive, preventive mindset. Leading indicators focus on behaviors and activities we are trying to encourage including:
- Performing risk assessments (identifying potential workplace hazards)
- Participating in safety training
- Reporting near-miss incidents, and
- Responding to the recommended improvements from our ECAP audits.
Our Performance
Among our Key Performance Indicators for workplace safety are well-recognized industry measures: the Total Recordable Injury Rate (TRIR) and the Total Vehicle Accident Rate (TVAR). The TRIR is the rate of injuries per 100 full-time workers. The TVAR is the number of accidents per million miles driven. For Nalco in 2011, the TRIR decreased by 25 percent from 2010. At 0.43, this was the lowest TRIR in Nalco history and exceeded our target of 0.48. This placed Nalco among the top 25 percent of companies in our industry. The TRIR has decreased more than 49 percent since 2007.
The TVAR for Nalco dropped 8 percent from 2010 to 2.1, exceeding the goal of 3.0. The TVAR has improved for three consecutive years and declined by 47 percent since 2007. Nalco also tracked the Severe Vehicle Accident Rate (SVAR) which measures driving accidents resulting in death, bodily injury, disabling or rollover of a vehicle. In 2011, the rate improved 8 percent to 0.22, exceeding our goal of 0.27. It has improved 63 percent since we began tracking the measurement in 2008.
The Ecolab TRIR improved 9 percent as well, decreasing to 4.25 in 2011 from 4.67 in 2010. This represents 47 fewer injuries. The TRIR has decreased by 11.6 percent since 2007. The TVAR for Ecolab was 6.2 in 2011, a 6.7 percent improvement from 2010 and a 15.3 percent improvement since 2007.
Additional information on our performance can be found in the Detailed Appendix to this report available at www.ecolab.com/csr.