Essity First To Produce Tissue in a CO2-Free Production Process Using Renewable Hydrogen
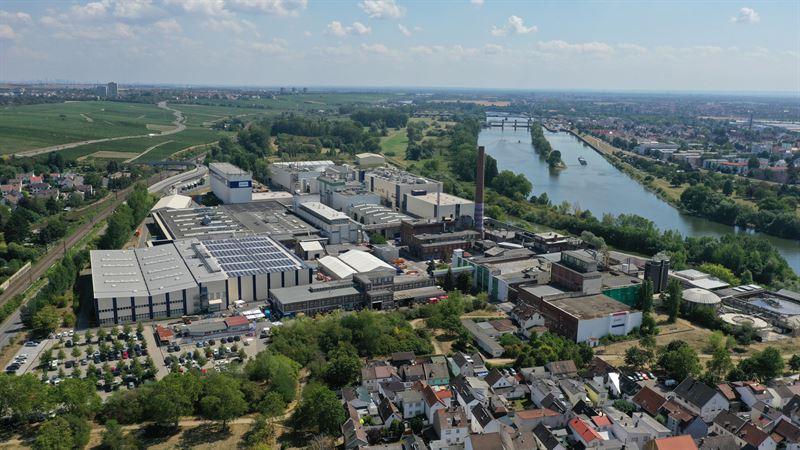
Originally published on Essity News Center
Hygiene and health company Essity has made another breakthrough on its journey to net-zero emissions by 2050. In a recently concluded pilot, Essity became the first company in the industry to produce tissue in a CO2 emission-free production process using renewable hydrogen at its production facility in Mainz-Kostheim, Germany.
Essity initiated the pilot for CO2-free tissue production in the second half of 2021. The pilot, encompassing efficiency programs and electrification through renewable energy, used hydrogen as a final building block to replace natural gas in the hood dryer of the papermaking process. As a result, Essity has successfully achieved a CO2-free production process for tissue.
“With this initiative, we have become the first in the world to use renewable hydrogen for tissue production. This is a major milestone in our ambitious climate agenda and a big step toward a decarbonized society. We are creating a sustainable process that is setting a new benchmark for the industry,” says Donato Giorgio, President of Global Supply Chain at Essity.
Up until now, the paper drying process has relied on natural gas to achieve the required high temperatures of 600 degrees Celsius. Renewable energy has not been a viable alternative in this part of the process. By using hydrogen in the drying process, Essity has demonstrated that energy-intensive production processes can also become CO2 emission-free. The company aims to continue applying breakthrough technologies to significantly reduce its environmental footprint.
Essity’s plant in Mainz-Kostheim has a strong focus on sustainability and circularity, transforming recycled paper into high-quality tissue, marketed under the company’s leading Tork brand. A total of 152,000 tons of tissue are produced at the production facility each year.
Read more about Essity’s journey to net zero here.