Getting Back on the Landfill-Free List
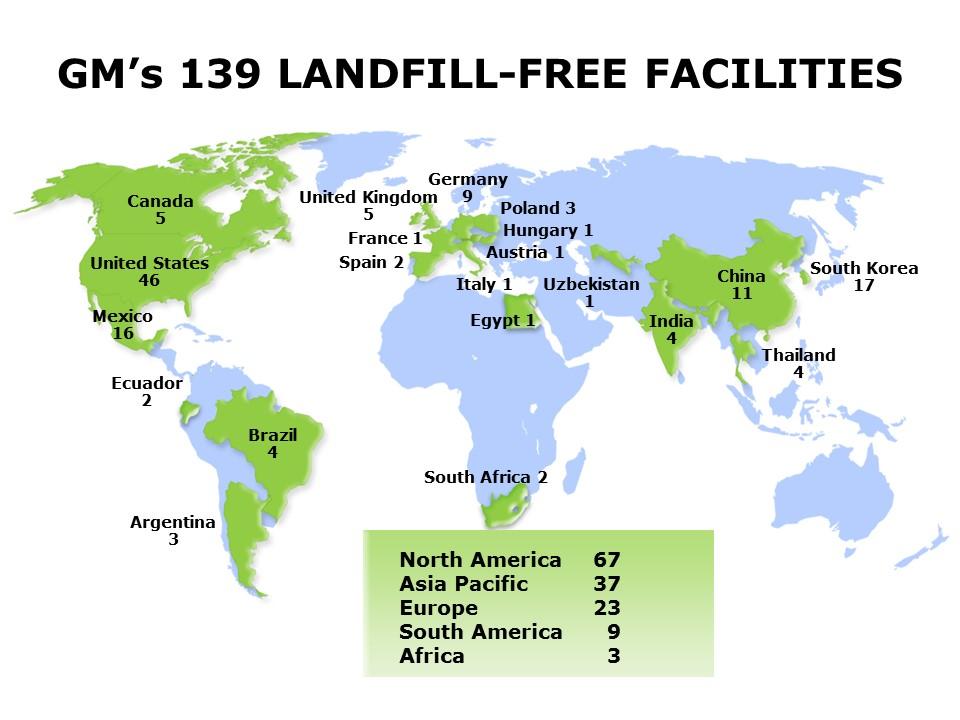
Getting Back on the Landfill-Free List
General Motors’ expectations for a landfill-free facility are structured and strict, with sites removed from the list if even a small load goes into the ground. When that happens, both the local teams and global waste experts collaborate to find solutions.
GM’s manufacturing plant in Cairo, Egypt lost its certification in 2015, but worked hard to get reinstated. As of this summer, the site is landfill-free once again.
The culprit was paint sludge—the sticky leftover residue from painting a car. While GM has turned paint sludge into pallets at some of its U.S. plants, it’s largely an issue of recycling infrastructure availability. The material can be used as an energy source to create cement, but the logistics of sending it to such a facility in Egypt became cost prohibitive.
After some brainstorming, they began talking with another partner – one that already managed the plant’s medical waste. This company was willing and able to handle this waste given its experience managing complex substances. The company developed a process to clean out the sludge and oil residue from the containers and convert the residue to energy. The containers were then sent to a recycler.
The result is a supplier that was able to add onto its capabilities and take on the waste stream after securing all necessary government approvals. The resulting partnership also brought cost savings to the plant.
Plant leadership in Cairo then established a back-up with another partner who could handle the waste should something come up with the first option.
“This was not a quick process; it took about eight months of planning and supplier negotiations,” said Aly Hassan, environmental manager at the Cairo facility. “In the end, we’re better for it and it strengthened our team.”
GM’s landfill-free operations are relatively balanced throughout the globe, partly because of the best-practice sharing among facilities. In this case, sustainability and supply chain leaders from Detroit spent time discussing options and working through various solutions with the Cairo manufacturing and environmental teams.
“We’re all in this together,” said John Bradburn, GM’s global manager of waste reduction. “We have monthly calls with our environmental engineers around the globe to discuss challenges they encounter and we regularly share resources to help advance GM’s environmental performance.”
The Cairo plant is planning ahead to further improve its waste management processes. Their resource managers rely on data showing how much and what kind of waste comes through the plant to identify opportunities for creative reuse or recycling projects.
Designing out waste is the ultimate goal, so another priority is to influence packaging decisions. This particular site receives pressed metal, engines and other powertrain parts for the site to weld together. Greater efficiencies in packaging not only reduce waste, but also contribute to shorter lead times.
With Cairo back on the list, GM’s new landfill-free total is 139. This includes other recent additions, such as two Michigan aftersales centers; two distribution centers in South Africa; a parts distribution center in Ecuador; and a powertrain plant, stamping facility and distribution center in Talegaon, India. The company is committed to achieving 150 landfill-free sites by 2020.