GM Employees Amp Up Efforts to Amp Down Energy Use
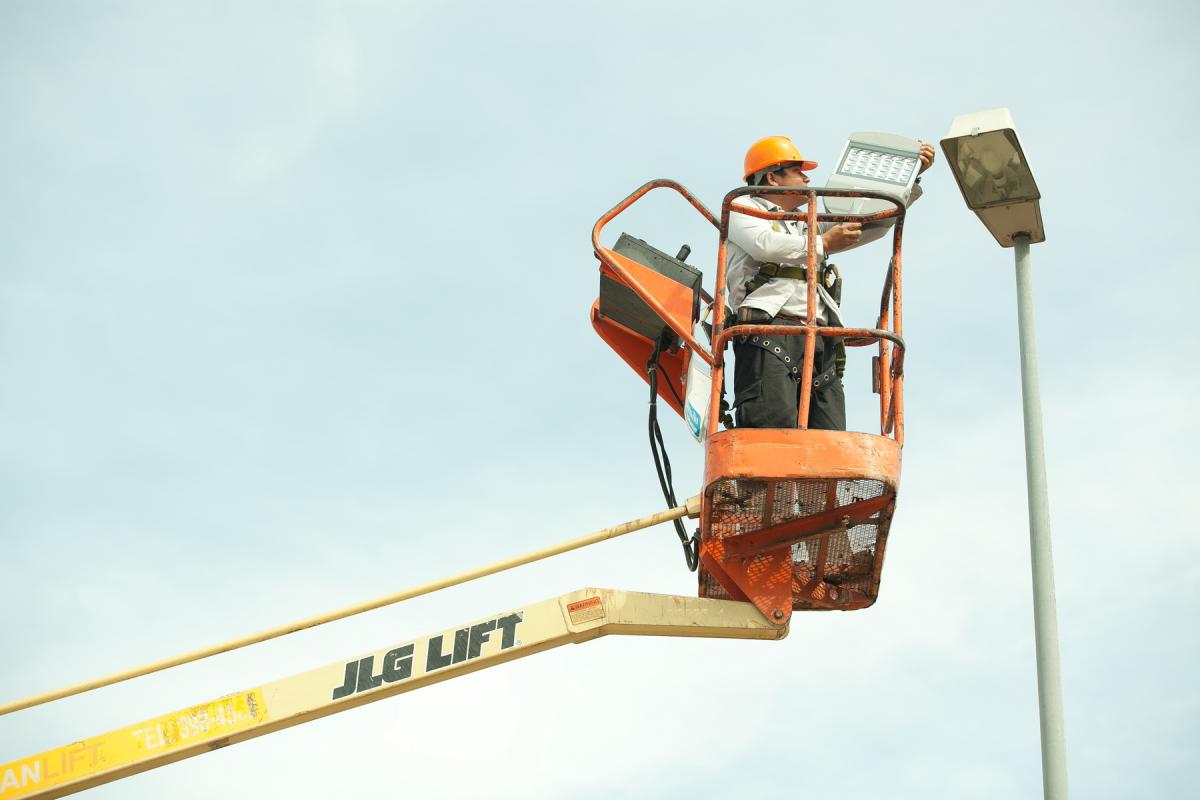
Imagine a 66-year-old assembly plant that competes with the newest builds when it comes to energy efficiency.
Our Flint Assembly plant, one of 63 plants to meet the U.S. EPA ENERGY STAR® Challenge for Industry, is the oldest in the GM family and proof that you don’t need to start from scratch to meet an energy efficiency challenge.
And at General Motors, we love a good challenge.
Today, we are announcing 63 of our plants have voluntarily cut energy intensity by at least 10 percent within five years – resulted in a collective avoidance of $162 million in energy costs and a reduction of 1.6 million metric tons of CO2 – equivalent to the electricity use of 244,000 homes.
GM’s environmental commitment, combined with the ingenuity of all of our employees, makes for more efficient operations that save us money and lessen our carbon footprint.
Of those 63 plants, nine are new additions and 22 are repeat achievers, which means they met the Challenge again after being recognized the first time.
Here are some of the ways in which our plants reduced energy use:
- Our Rayong Assembly Plant in Thailand installed skylights in various shops to harvest daylight.
- St. Petersburg Assembly employees in Russia installed devices that control consumption of various energy sources and developed procedures that decreased equipment start-up time, lessening energy wasted before work begins.
- Flint (Mich.) Assembly upgraded its lighting and cut steam heat for cost and carbon reductions.
We have more facilities that met this EPA Energy Star Challenge for Industry than any other company worldwide. Our 63 facilities represent 42 percent of our global manufacturing operations.
Tim Lee, executive vice president, Global Manufacturing and chairman of GM China, sums it up:
“Creativity and energy management go hand-in-hand at GM. We’ve been consistently cutting energy use and emissions each year, requiring us to dig deeper for innovative paths to energy savings. Environmental responsibility – and its corresponding business benefits – continues to be an everyday driver within our facilities.”