GM’s Energy Stars: Bob Griffith, Spring Hill Manufacturing
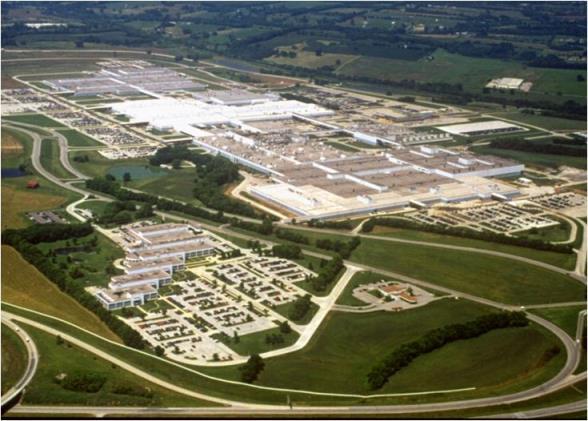
All this week we will be recognizing GM employees from across the globe who helped the company achieve the U.S. ENERGY STAR Challenge for Industry earlier this year. Without their diligence and commitment to the goal, we wouldn’t be able to tout the fact that 63 plants across the globe have reduced 1.6 million metric tons of CO2 respectively.
Name: Bob Griffith
Title: Site Utility Manager
Facility: Spring Hill
Length of time with GM: 28 years
1. What are some of the ways your facility cut energy intensity to meet the ENERGY STAR® Challenge for Industry?
We have replaced both metal halide and high pressure sodium lighting with energy efficient lighting. We’ve improved the heating and cooling equipment controls with automation leads to more efficient output. We expanded our Energy Management System capabilities to reduce energy consumption, and the manufacturing volume per shift has increased, which means we get more out of the energy we are consuming.
2. What are some tips you’ve picked up from your colleagues in the United States/internationally that you have incorporated into your facility’s energy savings program?
Through networking with personnel at plants around the globe, we were able to confirm that our planned lighting and HVAC project proposals had proved effective at other facilities. This gave us the peace of mind we needed to move forward.
We also try very hard to communicate energy use in terms that our employees can understand, like energy used by an average home, or the effect of energy on cost per unit produced. Our goal is that, if it’s easier for employees to understand, they are more apt to be energy efficient.
3. How do you engage employees to cut energy use in their day-to-day work?
We provide weekly reports that highlight our energy use, including weekend shutdown reports with corrective actions that need to be taken. Furthermore, we highlight monthly energy performance that is specific to each business unit so they can see how they stack up to other groups at the plant.
4. What are some of the benefits you have seen at the plant since reducing energy usage by 25 percent?
With an upgrade in lighting comes an upgrade to our employee’s work spaces, as well. Better lighting improves the work our employees do every day. With upgrades to the HVAC system, our employees are more comfortable when it comes to temperature, and we get fewer calls regarding our heating and cooling system.
5. What are some energy savings tips that you take home with you at the end of your day?
I have upgraded to energy efficient systems at my house when working on home improvement projects, including the installation of a geothermal pump, metal roofing and energy efficiency lighting.