The Gorton’s Fisherman Trusts Oil-Free Air
Sustainability drives compressed air upgrades at major seafood facility
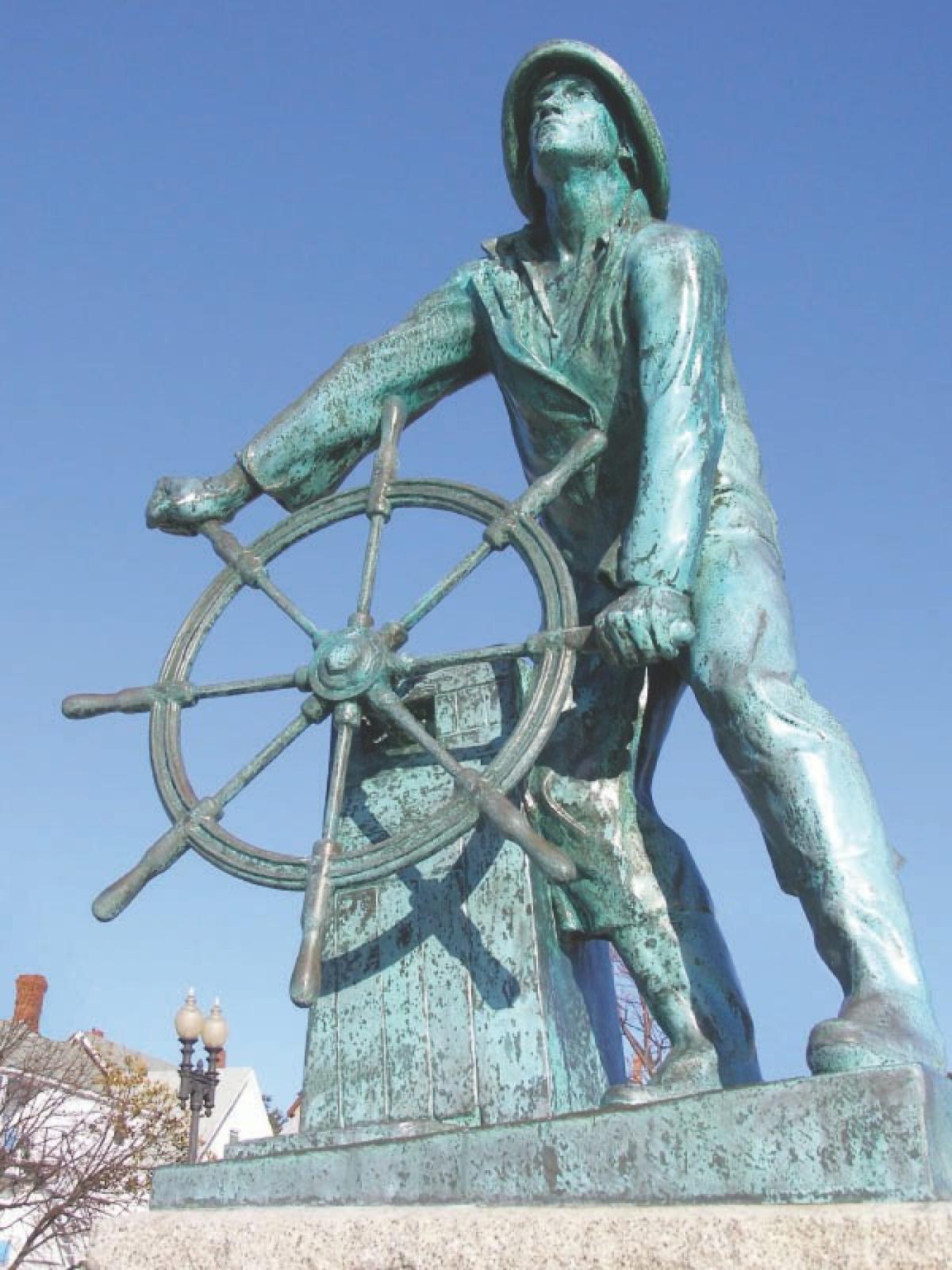
Atlas Copco | Innovation Stories 2016
Perhaps more than any American city, Gloucester, Massachusetts is synonymous with fishermen. The oldest seaport in the United States, c. 1623, Gloucester rises above a natural harbor flush with postcard-perfect scenes of fishing boats and the men who make their living at sea. For countless generations, fishing has been the lifeblood of Gloucester. It’s so engrained in local culture, even the city’s high school sports teams are called The Fishermen.
Along the waterfront, the Gloucester Fishermen’s Memorial stands watch, paying homage to “They that go down to the sea in ships.” The memorial is a tribute to more than 10,000 Gloucester fishermen who have lost their lives at sea over the centuries and a reminder that fishing is our country’s most dangerous occupation. The memorial includes the famous statue known as “The Man At The Wheel,” which was commissioned for Gloucester’s 300th anniversary in 1923.
Even if readers have not seen the statue of The Gloucester Fisherman in person, they probably have seen its likeness many times in their homes (in their freezers to be precise). That’s because the image of The Man At The Wheel is the logo of Gorton’s, the seafood products company.
Founded in Gloucester in 1849, Gorton Fisheries was a pioneer in the U.S. fishing industry. Today, Gorton’s is a world leading seafood processor and an organization committed to sustainable seafood production. The company is also focused on green efforts aimed at continually improving efficiencies in their processing facilities.
David Gazda, Operations Manager for Gorton’s, Inc., had been working on a project to upgrade the compressed air system at Gorton’s main plant in Gloucester. “We had it in our capital plan to replace our three reciprocating compressors and had met with our primary supplier who we’d worked with for at least 30 years. We were kicking the tires on their newest rotary screw compressors that use food-grade lubrication.” At this time, Dave attended an industry trade show in Chicago and first met with representatives from Atlas Copco. “When I stopped by the Atlas Copco booth, I was introduced to something new to me, the integrated design concept. The variable speed drives, air dryers, and ancillary components were built right into the compressor packages. The equipment proposed by our existing supplier was not integrated. I decided to find out more.”
Ron Whelan, Sales Manager - Oil-free Air and Key Accounts with Atlas Copco Compressors LLC in West Springfield, Massachusetts, connected with Gazda to discuss the proposed project. “When I inquired about their application – seafood processing – I started talking about the advantages of oil-free air,” Whelan recalls. “Dave Gazda had explained that they were going with an oil-lubricated compressor. I said that I’d be glad to quote an oil-lubricated system so he’d have another price, but there’s a better mousetrap I suggested he should also consider.”
Whelan introduced Gazda to the Atlas Copco 100% oil-free Z compressor. Oil-free compressed air is a natural for any food related industry as it completely eliminates the potential for product contamination from lubricating oil in compressed air. The oil-free Atlas Copco Z compressor is a two stage, rotary screw machine that has been the industry leader for over 40 years. There has never been a single case of downstream oil migration from a Z compressor.
Gazda immediately favored the security offered by an oil-free machine but was concerned about the energy cost. Whelan explained that the Z compressor is unparalleled in that regard. “The Z compressor can be supplied with integrated variable speed drive to match the energy cost directly to the compressed air load at any time, ensuring the absolute lowest cost to produce air. The cream on top is that the Z can also be supplied with a built in MD dryer for virtually free air drying.” The unique MD dryer uses the heat generated during air compression to regenerate a rotating desiccant drum. The only power consumed is for a small gear motor (1/8 HP) and there is zero purge loss.
Whelan arranged a tour at another customer, a dairy processor up the coast, so Gazda could see an oil-free air installation. Whelan then calculated the energy consumption of Gorton’s existing compressed air system and the savings projected for both the oil-lubricated solution and the oil-free Z/VSD/MD system. He presented the figures to National Grid, Gorton’s electric utility, for incentive consideration. “The energy savings from the Z/VSD/MD package was significantly higher than the oil-lubricated equipment that Gorton’s had been considering, so it qualified for a larger incentive from National Grid,” says Whelan. “When the larger incentive was factored in, the net price difference between oil-lubricated and oil-free systems was marginal.”
Gazda agrees that oil-free compressed air makes sense for food processing. “Compressed air comes in contact with product, so we don’t want lubricating oil in the airstream,” Gazda says. “It’s not part of our ingredient legend. Gorton’s went oil-free because we want to use the best quality air possible. Also, regulatory changes are continually changing and we want to be prepared to always meet the highest standard for food quality and food safety.”
While large food processors typically have oil-free compressed air systems or are in the process of upgrading, Whelan points out that some medium-size and growing companies have been hesitating. “They’re postponing the inevitable,” he explains. “They use food grade oil in lubricated compressors as a cheaper alternative to 100% oil-free. The problem is, food grade oil is made by starting with a solid formulation of oil and then removing the good lubricating ingredients. Food grade oils break down much quicker, are more sensitive to hot environments, and require more frequent change intervals, several times per year typically. This increases the maintenance cost as well as the hassle, expense and environmental concerns of disposing the waste oil properly. In an operation that runs 8,600 hours a year, oil-free air is superior, hands down. Food processors that are still using oil-lubricated compressors need to be thinking seriously about migrating to oil-free air while they are still in control of the decision.”
When Gorton’s factored in all the relevant facets of the project, it became clear that oil-free air was the way to go and Atlas Copco offered the optimum equipment solution.
Phase 1
As Gorton’s moved forward with its plan to upgrade their compressed air system, the first step was to replace the existing compressors supplying air to pneumatic systems around the plant. “Gorton’s had three reciprocating compressors that were close to 40 years old,” according to Whelan. “Two were 150 hp units and the third was 100 hp. There were no integrated dryers, so each compressor had its own independent dryer as well. That quagmire of equipment was replaced by three Atlas Copco Z/MD systems, each housed in a compact, fully-integrated cabinet. The lead machine has energy efficient, variable speed drive control and will trim the load at all times, maximizing efficiency. A new Atlas Copco ES series sequencer controls the operation of all three machines. This equipment is vastly more energy efficient, much quieter in operation and far more reliable. It takes up less space and looks much better, too”
Phase 2
The next part of the project involved Gorton’s five ADF freezers. “Dry air is crucial in our freezers,” says Gazda. “A rise in dew point could freeze the coils and negatively impact product quality.” Each of Gorton’s ADF freezers had a separate, stand alone, heatless desiccant dryer to lower the compressed air dew point to -40F. This type of dryer requires frequent regeneration using compressed air purge to remove moisture adsorbed from the output airstream. While this setup is effective, it is not very efficient as a great deal of electricity is consumed to produce the large volumes of compressed air used for the purge.
“With the new Atlas Copco compressors and MD dryers, we are running well below the -40°F dew point we are used to,” according to Gazda. “Still, there could be times, if it got really muggy, that we couldn’t be 100% assured of achieving the low dew point we must have.”
Whelan designed a solution to ensure the low dew point air that Gorton’s requires for the freezer – even during periods of high ambient humidity – with minimal power consumption. “With an Atlas Copco MD dryer, air coming out of the compressor is already very dry,” Whelan explains. “To be absolutely certain that the dew point would always meet the specified level, I recommended an Atlas Copco AD300 heated trim dryer to polish the air before the freezers.” The AD application is perfect after an MD dryer since the unit can stay on line for weeks at a time before requiring full regeneration and the accompanying purge loss.
“Probably 95% of the time we don’t need the additional drying,” according to Gazda. “But our freezers absolutely need -40°F air, so provisions are now in place with the polishing dryer.” Gorton’s went from five heatless desiccant dryers that consumed large volumes of compressed air for frequent regeneration, to one zero-purge MD dryer supported by one AD polishing dryer. The MD/AD combination reduces Gorton’s annual electrical consumption by 44,000 kWh or $8,000 per year. This project was also submitted to National Grid and qualified for an energy incentive.
Phase 3
Gorton’s further enhanced its sustainability efforts by incorporating Atlas Copco’s Energy Recovery Option into their new Z compressors. Compressing any gas, including air, produces heat. This heat is typically wasted to the atmosphere through a cooling fan for air cooled compressors or a cooling tower for water cooled compressors. Atlas Copco engineers devised an innovative system that captures the wasted heat of compression so it can be reused in the form of discharge hot water off the compressor package. The water temperatures are adjustable and can be set as high as 190F.
“We ordered our Z compressors with the Energy Recovery Option built in with the intent to use the hot water down the road,” says Gazda. “Right now we are running the compressors with the standard cooling method. We calculated that there are about a half million BTUs available in these machines that we will be able to use for hot water, sanitation water, building heat or pre-heating an oil boiler. These opportunities currently exist in our plant and we plan to start feeding them as soon as we can apply the appropriate engineering resources to the task. Ordering the machines today with Energy Recovery means that we don’t have to design and purchase an entire recovery system down the road. We simply have to turn on the option in our compressors and then connect to our applications.”
The net result of Energy Recovery implementation will be a reduction of natural gas consumption, yet another step on the sustainability path at Gorton’s. “National Grid is also our gas supplier and they have incentive programs for gas conservation projects as well,” says Gazda. “They have stated their willingness to participate financially in the project and we can’t wait to allow them to.”
Gorton’s investment in oil-free air is already improving productivity, reducing operating expenses and supporting the company’s ongoing efforts in sustainability. “Now we have very efficient, very reliable compressors plus a maintenance package, so we’re pretty autonomous,” Gazda concludes. “I would totally recommend Ron Whelan and Atlas Copco. I already have.”
About Gorton’s
Gorton’s was founded in 1849 in Gloucester, Massachusetts, America’s oldest seaport. Today, Gorton’s is committed to protecting and enhancing the sustainability of seafood resources and is working actively to support this under its Trusted Catch program. Trusted Catch encompasses all of Gorton’s sustainability initiatives, from sustainable seafood sourcing to other green efforts including a more efficient plant and distribution network.