Health and Safety Considerations in 3D Printing
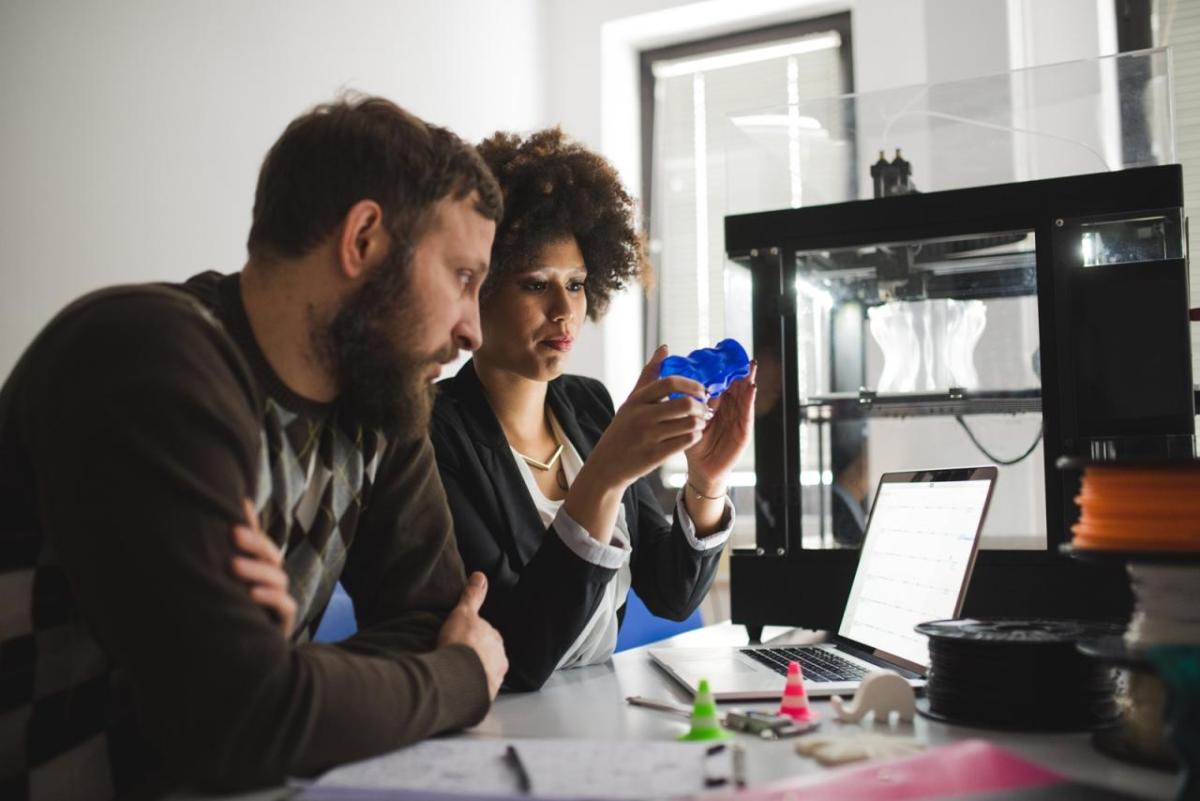
The ability of 3D printing technology to rapidly turn digital blueprints into complex physical objects has revolutionized production processes across industries ranging from manufacturing to medical.
However, as 3D printing’s role in these sectors grows, it brings with it a number of health and safety challenges. From chemical exposures to physical hazards, this post explores the health and safety risks tied to industrial 3D printing operations, and offers best practices EHS professionals can share with their workforce.
Health Risks Associated with the 3D Printing Process
3D printing, also known as additive manufacturing, enables the production of three-dimensional objects through the repeated layering of amorphous material that is cured into a solid. This technology is used as both a prototyping tool and a mainstream manufacturing technology across multiple sectors.
Due to the nature of the process, there are a number of inherent health risks associated with 3D printing.
Chemical hazards
- Polymers: Commonly used polymers like ABS (Acrylonitrile Butadiene Styrene) and PLA (Polylactic Acid) can emit styrene and lactide during printing, which are compounds of concern if inhaled in significant amounts.
- Additives and specialty resins: These materials often enhance the properties of printed objects but may contain hazardous chemicals that require careful handling and disposal.
- Soluble support materials: Some printing processes use support structures that are removed via chemical baths. Materials like PVA (Polyvinyl Alcohol), which is used for these purposes, can require special handling to prevent skin contact and respiratory exposure.
Physical hazards
- UV exposure: Printers that cure materials with UV light can pose a risk of skin and eye exposure to ultraviolet radiation.
- Electrical risks: As with any electrical equipment, there is a risk of shock or fire, particularly if devices are high voltage or improperly maintained or handled.
- Equipment temperature: High temperatures are necessary to melt printing materials, placing operators at risk of being burned.
- Moving parts: Automatic feeds and moving parts of the printer can pose entanglement or pinch hazards, especially when maintenance or troubleshooting is required without proper lockout procedures.
Particulate and fume emissions
- FDM printers: Fused deposition modeling printers melt plastic materials, emitting particulates and potentially toxic fumes, especially in poorly ventilated spaces.
- SLA Printers: Stereolithography involves resins that can release volatile organic compounds (VOCs) during printing, which are hazardous when inhaled.
Noise exposure
Depending on the size and type of printer, the noise level can be substantial, potentially leading to hearing loss over prolonged exposure periods without adequate hearing protection.
Managing Health and Safety Risks in 3D Printing
The following are best practices for handling the various hazards associated with 3D printing technology.
Ventilation and air quality
Proper ventilation is, perhaps, the most crucial health and safety concern to address, due to the risks posed by both chemicals and particulates present in the 3D printing process. Having a robust ventilation strategy is essential for minimizing exposure.
- Local exhaust ventilation (LEV): Installing LEV systems at the source of emissions can capture most airborne contaminants before they spread into the workplace environment.
- General ventilation: Enhancing the overall air turnover in the room helps dilute the concentration of airborne contaminants. This is particularly important in enclosed spaces where multiple printers are operating.
- Air filtration systems: High-efficiency particulate air (HEPA) filters can effectively trap fine particles, while activated carbon filters are good for reducing gas and vapor concentrations.
Personal protective equipment (PPE)
Using appropriate personal protective equipment is critical for minimizing exposure to hazards.
- Respiratory protection: Use respirators or masks certified to filter out particles and fumes associated with the specific types of materials being printed.
- Eye and face protection: Safety goggles or face shields should be used to protect against splashes, dust, and debris.
- Gloves: Gloves that are resistant to the specific chemicals used in the printing materials should be worn to handle materials and operate equipment safely.
- Protective clothing: Long sleeves and aprons made of suitable materials can help protect skin from chemical exposures and burns.
- Hearing protection: Provide earplugs or earmuffs to workers operating in environments where decibel levels are high due to printer operations.
Material safety
Safe handling and storage of materials are essential for preventing accidents and health issues.
- Material handling protocols: Implement strict guidelines for handling chemicals and raw materials, including the use of appropriate tools to minimize direct contact.
- Storage solutions: Store sensitive materials in cool, dry places away from direct sunlight and heat sources. Ensure that all containers are clearly labeled and securely closed.
- Waste management: Establish procedures for the proper disposal of waste materials and unused residues, including recycling options where feasible, to minimize environmental impact.
Equipment safety
Scheduling and documenting regular maintenance inspections ensures that equipment remains in optimal working condition. Comprehensive training for all operators empowers workers to handle equipment safely and effectively. Clear signage should also be used to highlight potential danger points on equipment, helping to remind and educate staff about risks and proper handling procedures.
Organizations that leverage 3D printing technology must prioritize the health and safety of their employees and customers above all.
Learn more about Antea Group's EHS resources and services.