How To Grow a Sustainability Pilot Into Reality at Scale
Words by Miranda Gardiner
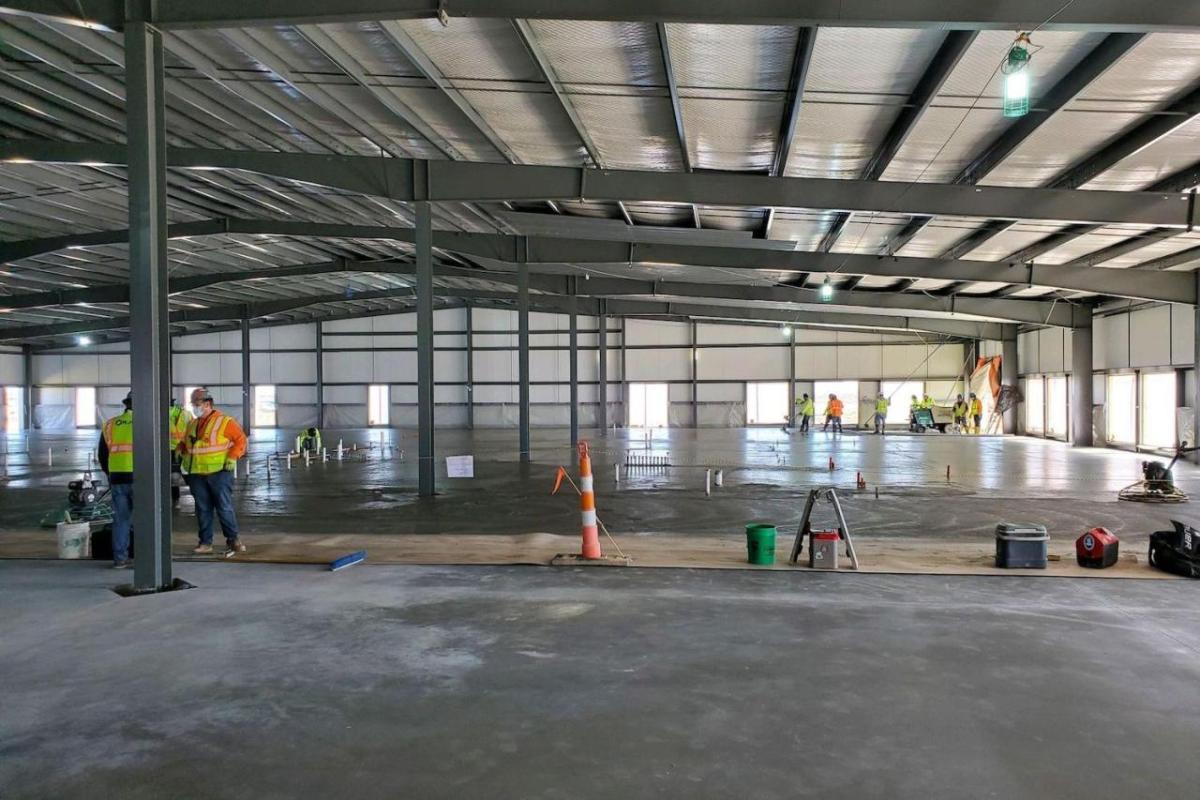
Originally published on TriplePundit.com
Meta data centers are among the most advanced, energy-efficient in the world. Despite their enormous footprint, however, these structures are designed with the respect of our land, our communities, and our people in mind by incorporating design and construction strategies that conserve energy and water, eliminate waste, and responsibly source materials. The result: Our facilities are LEED Gold certified and supported by 100 percent renewable energy.
To drive innovation and efficiency beyond these high standards, our team has multiple pilot programs in various stages of pursuit and delivery. They vary from experimenting with low-carbon concrete and tracking the circular economy of materials, to testing the feasibility of an all-electric construction vehicle fleet and sourcing alternative fuel sources. Yet they are united by one goal: to create future data centers on the cutting edge of performance and sustainability.
A successful pilot means not only securing buy-in from internal stakeholders, along with funding and manpower, but also mapping a path to applicability and scalability across the enterprise. When it comes to determining whether a pilot is viable, our team begins with a five-factor framework:
- Impact: What is the impact of this strategy?
- Application: What is the universality of the pilot?
- Engagement: How will we communicate, with various stakeholders, a message that will most resonate?
- Prioritization: Where will this fall in the line of current and future projects/initiatives?
- Funding: What is the cost (money, time, effort, education/training) to implement?
These questions help us shape each pilot and support higher-level focuses, such as reducing Meta’s carbon footprint. When Meta’s Net Zero program was in its infancy, for example, we strategized pilots to test new technologies and approaches to track the impacts of material composition in our mechanical, electrical and plumbing equipment; our facilities’ operational waste; and potential of alternative fuel types.
In 2021, we proposed HVO (hydrogenated vegetable oil) as a carbon-saving alternative to diesel for construction equipment at one of our European facilities. The site had regional availability of the fuel type, plus the application and contractor partner were deemed a good fit. Ultimately, timing and cost made the pilot too challenging to pursue. Fortunately, our team's extensive analysis on HVO provided the solid promise for a future opportunity with a greater understanding of a successful pilot proposal and further refinement of stakeholder engagement, as well as a new Risk Registry tool to identify potential risks in a project that can derail intended outcomes.
Today, those lessons have shaped an exciting pilot to test low-carbon concrete, the primary contributor to emissions from data center construction (and 8 percent of global emissions overall). Our pilot leveraged artificial intelligence (AI) to identify and test low-carbon concrete mixes and, ultimately, resulted in use at scale in our data center in DeKalb, Illinois, in 2022. In a partnership with the University of Illinois at Urbana-Champaign, we utilized AI to find a sustainable concrete mix with 40 percent lower carbon emissions. The team worked closely with our concrete trade partner, Ozinga, on test applications in non-critical areas to meet a combined goal of both low-carbon and long-term strength requirements.
It’s true that the carbon footprint during the data center construction phase can often be overlooked. To offset this, we work with our general contractors to communicate ways to reduce (and eliminate) the barriers to going green on a typical job site. Meta’s general contractors now implement technologies and processes for more efficient builds, linking to carbon reductions with partners and circularity in our materials. At our Altoona, Iowa, site, we are upscaling onsite tracking to include both construction and operational waste (as well as using hybrid-fuel construction equipment). It’s just one combination leading our builds to greater, sustainable impact.
Thanks to our robust and vetted piloting program, along with engaged stakeholders, we are able to build with successful social and environmental impacts while providing opportunities to integrate new technologies and strategies across our portfolio. We minimize risks across our facilities by testing ideas — whether a change in design or construction, or even a process — and gain wider acceptance before rolling it out for wide-scale application.
And thus, our work toward greater performance and sustainability continues to build.
This article series is sponsored by Meta.