Is Large-scale 3D Printing Sustainable?
by Kenneth Wong
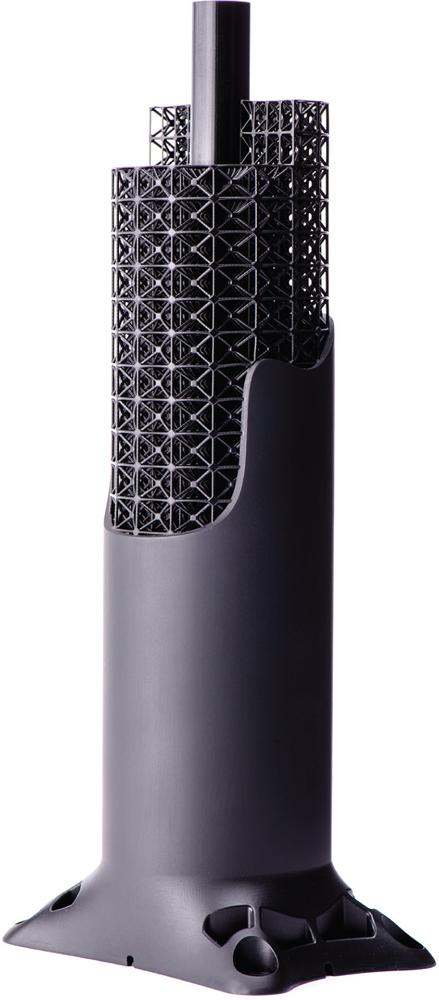
Originally published in the December 2018 issue of Digital Engineering magazine
With the introduction of its own 3D printing hardware line, dubbed Multi Jet Fusion (MJF), HP is expected to become a major player in the AM ecosystem as well.
“Our Multi Jet Fusion printers were created to be circular and sustainable right from the start,” says Nate Hurst, HP’s chief sustainability and social impact officer. “For example, both of the plastics that are used—PA12 and PA11—can also be recycled, both as a powder and as a printed part. HP’s 3D High Reusability PA12, which is developed to allow reuse of surplus powder batch after batch, delivers consistent performance while achieving 80% surplus powder reusability. In addition, we recently released a PA11 material that is a 100% bio-based content polymer derived from the oil of the castor bean. Castor beans are non-GMO, require little irrigation and are naturally pest- and drought-resistant.”
Sustainable and Strong
In April 2018, HP announced an initiative called “Reinventing HP with Multi Jet Fusion.” The company says it plans to “leverage its own 3D printing technology to lower costs, speed time to market, increase customer satisfaction and improve sustainability.” Accordingly, “HP is using Multi Jet Fusion across its print, personal systems and 3D printing business units.”
“In some cases, we’ve been able to replace metals or other plastic alloys, with a single material that will be fully recyclable and overall less mass,” Hurst says. “Using 3D printing to make parts for our own HP Latex printers, we have replaced an aluminum part with a 3D-manufactured nylon part, resulting in a 93% decrease in weight, a 95% reduction in GHG [greenhouse gas] emissions and a cost reduction of 50%.”