Lordstown is All-In With LED Lighting & Efficiency
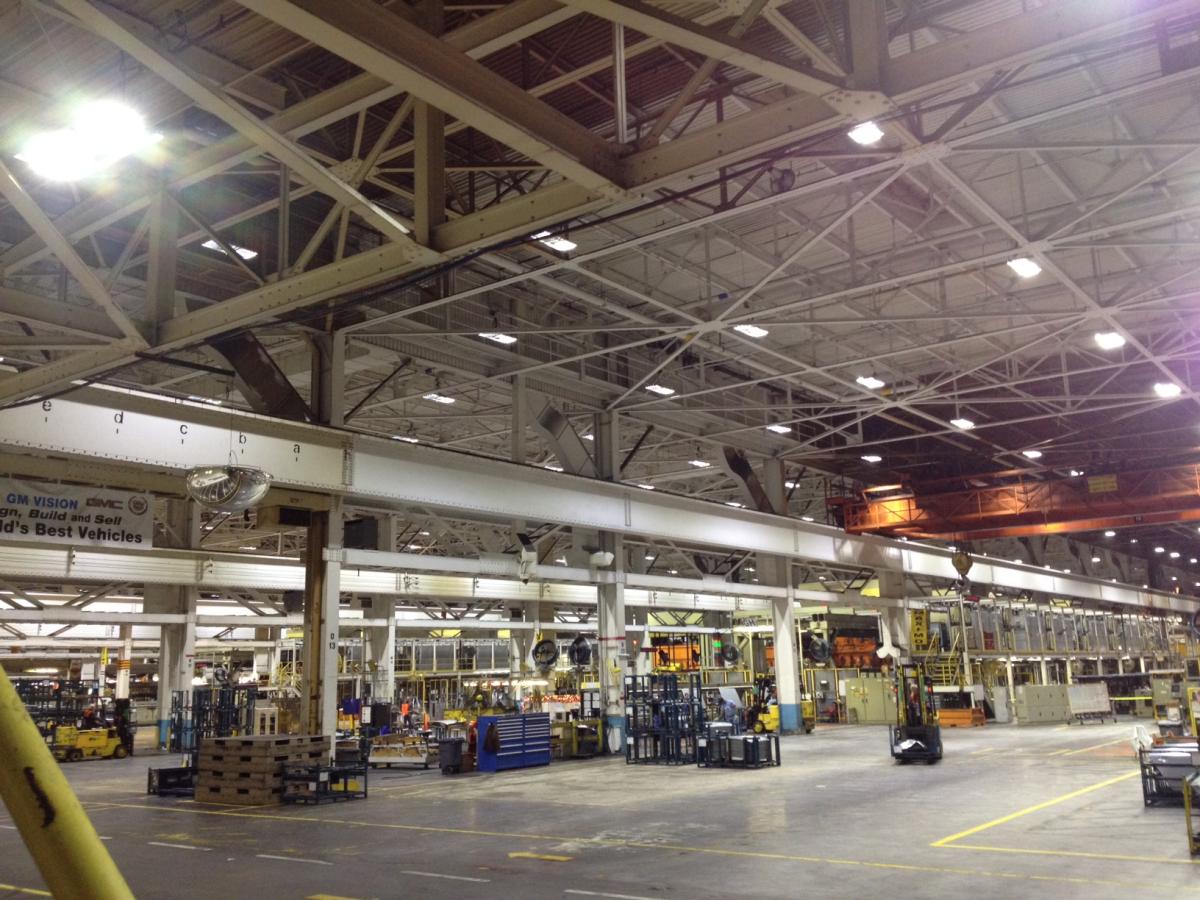
GM’s Lordstown Stamping plant is the first and largest North American GM facility to convert all of its lighting to high-efficiency LED bulbs. The switch will save the plant more than $800,000 overall annually, while reducing CO2 emissions by more than 8,500 tons. This is equivalent to annual energy use of 397 homes.
“Although replacing more than 1,600 light fixtures is a monumental task, we’ve now reduced the plant’s energy consumption more than 80 percent,” said Steve Rhoades, GM Lordstown Complex Manufacturing Engineering Director. “This project falls in line with Lordstown’s energy efficiency goals, as well as the company’s environmental vision.”
The LED fixtures are equipped with a fully-integrated and built-in wireless control system that was integrated into the General Motors Energy Management operating system. This allowed Lordstown to achieve even greater savings through scheduling of lights.
“We can now schedule our in-house lighting operating system with the push of a button, increasing output in designated work areas if needed, or dimming fixtures between breaks and shift changes,” said Rhoades. “As an added bonus of this conversion, we were able to remove all 1,280 fluorescent night lights.”
With the stamping plant project completed, the complex continues its plans to install additional efficient lighting. The adjacent west plant body shop has replaced 135 old fixtures with LED 120W low bay fixtures.
“With six million square feet of buildings and lighting throughout our complex, there is tremendous opportunity to become the benchmark in green energy solutions, and save a lot of money,” added Rhoades.