Operational Efficiency Builds Sustainable Future at Plymouth Mill
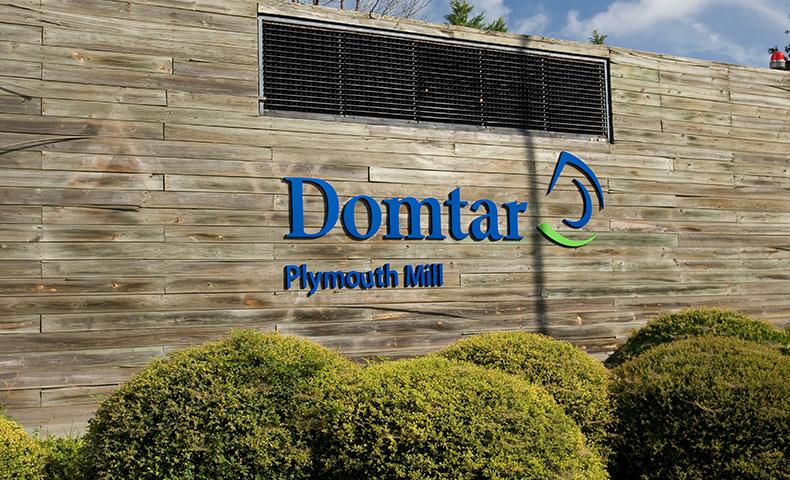
Visit Domtar Newsroom for more stories like this.
In 2017, Domtar set forth a vision to establish our pulp business as a growth driver for the company. Since then, the pulp leadership team has enacted tangible plans to optimize and improve operational efficiency at Domtar’s core pulp mills through a combination of capital investments and continuous improvement projects with the goal to grow the business into a world-class global supplier with strong long-term customer partnerships.
One such initiative is aimed at optimizing the Plymouth Mill’s operations in phases to grow it into a highly competitive pulp supplier. The first phase is focused on increasing energy and resource efficiency.
“We’re undertaking a number of energy and environmental sustainability initiatives to continue to reduce our overall energy footprint — effectively optimizing the mill to safely produce reliable pulp tonnage,” says Plymouth Mill Manager Allan Bohn. “All of those things will add up to streamlining the mill in terms of the number of energy assets we operate.”
A number of these operational efficiency projects will come to fruition in 2019. For example, the mill will save hundreds of thousands of pounds of steam per hour and several million gallons of cooling water per day by improving its fiber waste (hog fuel) boiler and installing a new cooling tower with heat exchangers.
Additionally, by eliminating the use of a biomass boiler that previously supported a recently retired pulp machine, the mill will consume less biomass to produce the same amount of pulp … not to mention the additional operational efficiency achieved through simplifying the mill to require less maintenance and general upkeep.
“We have a roadmap in place to reach our goal of operating a highly efficient mill,” Bohn says. “We’re working closely with our union partners to ensure we have the resources and structure to ensure a strong future for the mill.”
He says the organic continuous improvement actions have reduced chemical usage and energy consumption, and improved productivity — earning the mill the opportunity to grow those initiatives through company-funded investment.
“Over the last few years we’ve improved our efficiencies through these continuous improvement projects while still setting production records for slush and fluff pulp,” Bohn says. “These efforts have also had a tangible effect on our production bottom line.”
A stable bottom line driven by good cost position means continued viability for the mill, he says. “Our jobs are never done in finding efficiency gains, and the efforts we’re making today position us well for the foreseeable future.”