Putting Purpose into Action: Product Stewardship
Excerpts from the 2020 Medtronic Integrated Performance Report
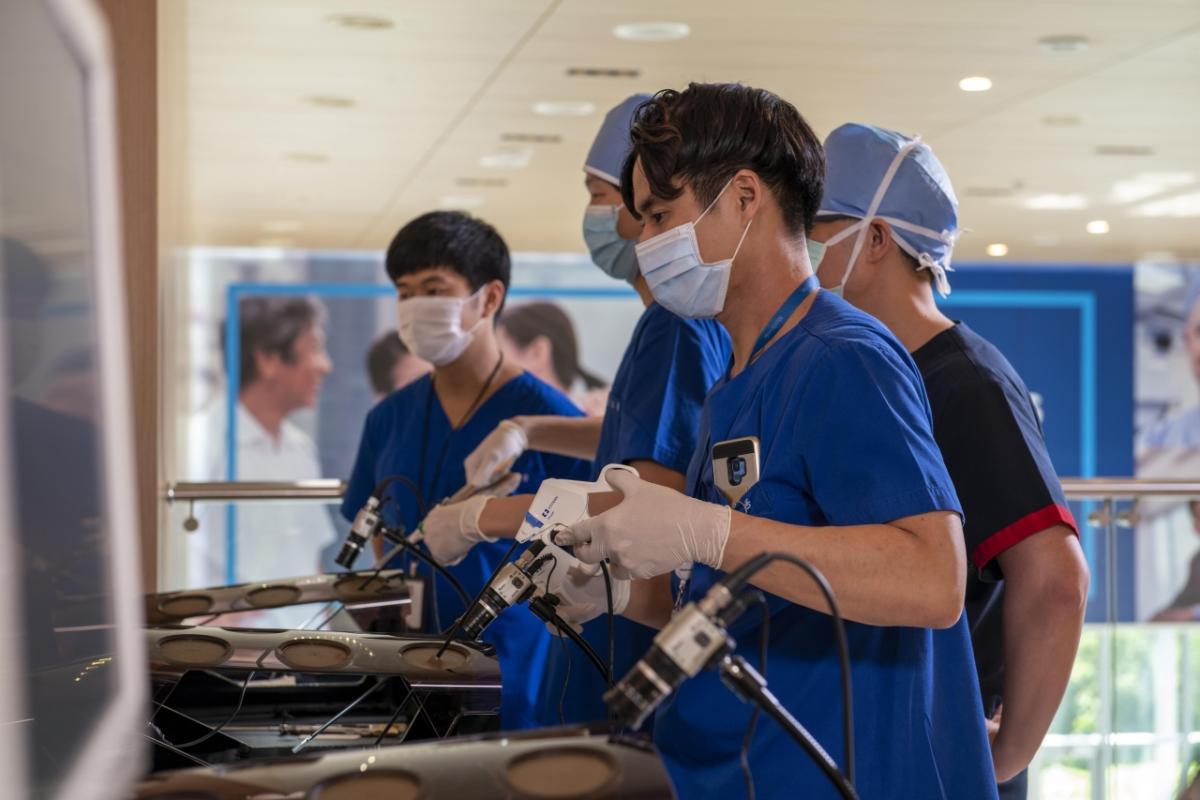
Putting Purpose into Action: Product Stewardship
ADDING BUSINESS VALUE
Patient safety is our absolute priority in manufacturing medical devices. This means we focus on quality, sterility, and compliance. Increasingly, in line with our customers’ priorities, we are also working to reduce the environmental footprint of Medtronic products and packaging.
DEVELOPING SAFE AND RESPONSIBLE PRODUCTS
A standardized approach helps us meet regulatory requirements for products and product communications. Our product stewardship and regulatory affairs teams manage our centralized process for monitoring the regulatory landscape and communicate requirements within the organization. Our scientists and engineers adhere to product stewardship guidelines when developing new products and have processes in place to meet a variety of product content requirements.
We are also prepared to meet the requirements of the E.U. Medical Device Regulation when it goes into effect in May 2021.
Materials of concern
There is growing concern about certain materials and chemicals in medical products, as demonstrated by emerging regulations and customer requirements. Materials of concern (MOC) include those that have the potential, if not managed correctly, to negatively impact people or the environment. We require our suppliers to responsibly manage and disclose any such materials used in our manufacturing processes, final products, or packaging.
In FY20, we launched our new Materials of Concern Policy to streamline the way Medtronic manages MOCs. Our activities included developing working teams to address a variety of ongoing product content matters and developing web portals to facilitate access to information.
Innovation is an important part of the Medtronic Mission, and Medtronic is proud to be a part of the U.S. Food and Drug Administration's (FDA) Innovation Challenge targeted to explore ways to reduce the amount of ethylene oxide (EO) used to sterilize lifesaving medical devices. Medtronic was selected in 2019 as one of several medical device companies to evaluate sterilization methods for the future. We are evaluating opportunities to streamline sterilization processes and decrease the amount of EO usage, in situations where it is possible to achieve equivalent sterilization effectiveness. Medtronic is developing strategic corporate partnerships and is engaged with the FDA to find effective solutions to deliver safe and sterilized medical equipment.
Product footprint and end of life
We are reducing the environmental impact of our products through product takeback and packaging initiatives. Where possible, we collect products for recycling, refurbishing, and reprocessing to give them a second useful life. Our initiatives include collecting:
- Nellcor pulse oximetry devices for recycling, reuse, and remanufacture
- MyCareLink heart monitors for refurbishing and redeployment
- Surgical technologies for energy generation from waste
In FY20, we collected more than six million products through takeback initiatives and diverted 250 metric tons from landfill.
In addition, Medtronic follows international guidelines and regulations for the disposal and recycling of electronic waste.
We also work with experts to create more sustainable packaging solutions. In FY20, our Cardiac Rhythm and Heart Failure (CRHF) Division partnered with CB2, a collaborative university-led group developing high-value products from agricultural and forestry feedstock. CRHF provided funding and research support to CB2 for a project on bio-based packaging that would be suitable for food or medical applications involving products that require sterilization.
The Medtronic Sustainable Packaging Working Group champions our efforts to integrate environmental factors into the packaging development process. One focus area is reducing secondary packaging — the packaging that protects but does not come into direct contact with products. In FY20, we redesigned the secondary packaging for three products, including two products that are used in minimally invasive spine therapy. The improvements to the spine products included removing an excess layer of barrier plastic and decreasing the size of product cartons. The changes yielded a 45%–85% decrease in package size among product SKUs. These enhancements improved sterilization while also reducing packaging landfill waste, shipping space requirements for transportation, and storage needed in healthcare facilities.