Solar Power Needs Silicon Carbide
by Ali Husain
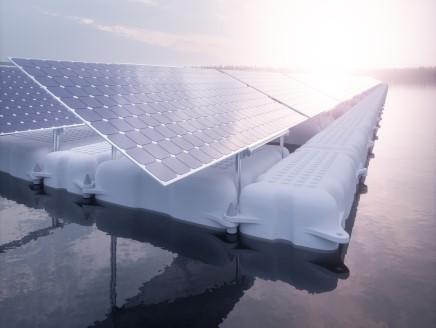
Read on the ON Semiconductor blog
Solar power is rapidly becoming a crucial piece of the electricity puzzle. Most people are familiar by now with the incredible 82 percent decline in costs for solar-generated power over the last 10 years. But many innovations in solar siting (where solar is located) and co-land use (what else the location is used for) are increasing the economic case for solar power. The most obvious location is on top of a building. Many retailers and warehouses with large, flat roofs add solar panels as an economic decision.
A twist on the co-use concept is the idea of floating solar panels. In this design, the solar panels are placed on a body of water so that it does not occupy precious land, and the water keeps the panels cool which increases the solar conversion efficiency. Some have even proposed floating the panels on a pumped hydro storage reservoir, with the panels providing the energy to be stored there.
Another example is called “agrovoltaics”, which is an idea to mount the panels maximizing space and allowing land below to be used for farming purposes. The solar panels are mounted high enough for equipment to go under and with adequate space so the plants get plenty of light. The plants actually benefit from the partial shade and the soil retains more moisture, saving water. Additionally, the panels run cooler due to the increased humidity below and, of course, generate clean energy from the sun.
Regardless of where you put the solar farm, it needs a power electronic converter to tie it to the grid. The converter consists of an optional voltage boost stage and an inverter to turn the DC electricity to AC synchronized with the grid. The efficiency of this conversion directly affects the economics of the project. Silicon carbide (SiC) is the next-generation power switch technology to improve the efficiency of the grid-tie, shrink the cooling system, and reduce overall system costs.
An important trend in solar power converters is increasing the voltage into the inverter up to 1500V. This will reduce the current needed for the same power, thereby reducing the size of the cables need to carry it.
Another trend is to move from a large centralized inverter to smaller, decentralized inverters that are much more easily maintained. This topology is more robust too because one failed inverter does not shut down the whole farm. For standardized, decentralized inverters, the designer tries to maximize the power within a fixed weight and size specification.
Silicon Carbide aids in providing higher efficiency for both of these trends. SiC devices are most useful for higher voltages compared with traditional silicon IGBTs. Higher voltage devices can simplify the topology, eliminating the need for multilevel converters.
SiC inverter solutions have lower losses than IGBT solutions. SiC MOSFETs are also faster switching, which can shrink the size of the passive devices, particularly the inductors. These two factors increase power density, allowing higher power in the same size and weight equipment.
ON Semiconductor has a full range of SiC devices for solar converters.
- Discrete MOSFETs and diodes in a variety of packages for flexibility
- Hybrid IGBTs with a SiC freewheel diode for cost optimization
- SiC Hybrid modules and full SiC modules for compact designs
We also offer an interactive block diagram to support your solar inverter design needs.