What Waste? Domtar Plant Achieves Its Zero-Waste Goal
From 2016 to 2018 , the Delaware plant made the journey from 80% to 100% beneficial reuse of its manufacturing byproducts.
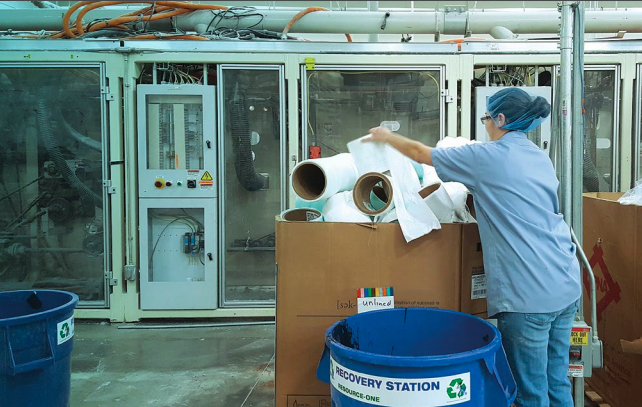
When Mark Clack joined Domtar in 2016 as the manager of the Delaware, Ohio, personal care facility, he noted that an impressive 80 percent of the manufacturing byproducts was being beneficially used or recycled. “Given Domtar’s commitment to sustainability, and my experience helping a microbrewery I previously worked at in California achieve zero waste to the landfill, I saw the opportunity to do the same in Delaware.”
In 2018, Clack’s goal for the Delaware facility became a reality. Delaware became the second Domtar manufacturing facility to reach the enviable milestone of sending zero waste to the landfill. Our facility in Aneby, Sweden, was the first.
This began with source reduction and keeping the recycling stream clean. Repurposing, recycling and waste-toenergy took care of the rest.
A key step was the reduction of scrap being generated by switching to larger-diameter rolls of raw material. The larger rolls run longer on the machine, resulting in fewer roll cores for disposal, saving time and improving efficiency of the line.
“Another important step was making it easier for colleagues to separate materials for recycling,” said administrative assistant, Vickie Bowles. Recovery stations were positioned closer to work areas so that sorting and recycling require less physical effort. Better signage and education also helped encourage participation.
Spent cores with remaining unusable raw material are now collected and shipped to InRETURN, an Ohio non-profit that employs people with traumatic brain injuries. Employees there reuse the material to make absorbent products such as dog beds, packaging materials, and more.
Non-woven materials, super absorbent polymer, paper, plastic and metal are separated at the facility and sent to specialized recycling facilities in the state.
Beneficially used or recycled 86 percent of the 19,812 metric tons of manufacturing byproducts generated at our personal care facilities in 2018.
The remaining residuals, including organic materials, are sent to a facility that generates clean energy for Indianapolis, Indiana.
Now all byproducts have found a second calling, keeping valuable resources cycling through the economy. Working together, our colleagues in Delaware have reduced the facility’s environmental footprint, doing their part to ensure a better future.
Read the 2019 Domtar Sustainability Report