Is Your Dairy Processing Plant Ready for Change?
How legacy dairy facilities can meet the challenge of modernization.
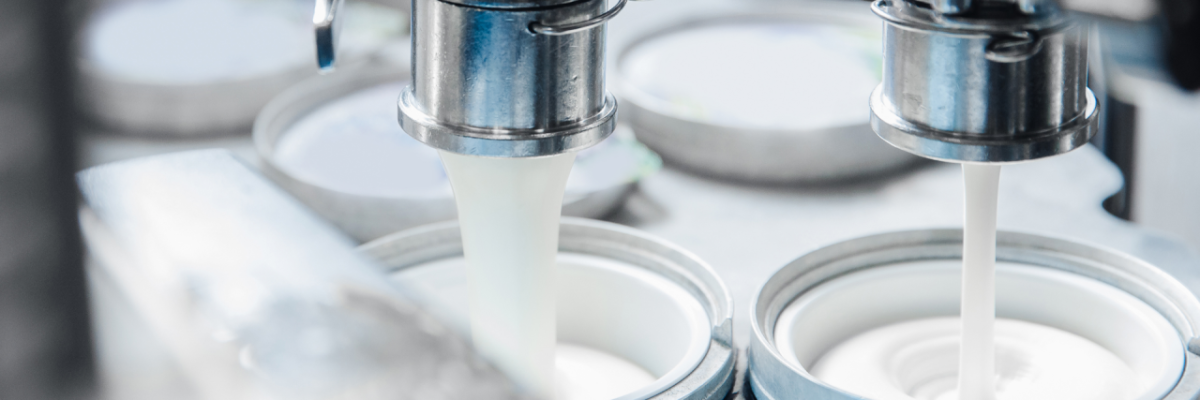
By Jason Tucker, Senior Process Engineer
Dairy processing plants are constantly improving and expanding to keep up with consumers’ ever-changing appetite for new products in the dairy aisle. The global dairy market is set to register a CAGR of 5.14% in the snack market alone during the forecast period of 2020-2024, thanks to demands for innovative, healthy, on-the-go dairy options.
Currently, we’re seeing many new products geared toward ethical eating, gut health, and other health-conscious offerings. Consumers are asking for high-protein yogurts, grass-fed sources, and cheese made with added vitamins and minerals—all delivered in portable and convenient packaging. At the same time, lactose-free dairy products continue to drive market growth, with yogurt and dairy desserts being the fastest-growing segments worldwide. Aseptic technology has made shelf-stable products for long-term storage possible, thereby reducing refrigeration and transports costs. Finally, demand from millennial consumers is driving adventurous options such as savory and spicy yogurt dips, flavored butter, and alcohol-infused ice cream.
Facilities are therefore challenged to scale production without sacrificing quality or safety. How can dairy processing plants keep up? The key lies in optimizing today’s operations while planning for tomorrow’s expansions. Here how.
Embrace a long-term plan for your dairy processing plant
Consumer demand and industry trends are driving facility and equipment changes and improvements. Since kneejerk responses can result in decisions made without consideration for future growth or expansion, it’s important to consider all the angles and lay out a long-term plan.
Assess future needs
What will your facility needs look like in the next 5 or 10 years? It might be hard to say with exact certainty, but dairy processing plant owners can consider what new products they’re most likely to add to their offerings. When incorporating new products, facilities should assess available space for ingredients storage, processing, packaging, and finished product storage. Appropriate levels of segregation to control allergens should also be considered as new flavors are added. Also, facilities need to plan how to handle packaging material waste from ingredients they add into products, such as salt, spices, and more.
Improve operations
The legacy plants built 50 to 60 years ago weren’t always built with efficiency and ergonomics in mind. As they expanded, small systems were often cobbled together. This kind of reactive, organic growth may leave process streams leaping over each other, risking the ability to properly segregate hygienic zones.
Good workflows are key to safe and efficient operations. Even small efforts to improve operations may increase throughput, improve time to market, and boost the bottom line. Lean operational solutions for a dairy processing plant could include:
- Improving workflows and product flows
- Managing waste routes for packaging
- Reducing/reusing waste (e.g. isolating proteins or water)
- Maximizing effective use of resources (e.g. heat or water)
- Addressing process variability
- Creating lean layouts
Leverage by-products
Dairy by-products, such as permeate and whey, represent an increasing market and, for some facilities, an untapped profit stream. Producers can build in flexibility by having multiple product lines all coming off the same source of skim milk to feed various outputs and produce a multitude of products. Of course, this kind of flexibility requires an investment in capital, square footage, and technology—but will open up new profit opportunities.
Whey byproducts—long used in protein bars and protein shakes—now form the majority profit share in some dairy facilities. According to Innova Markets Insights’, the number of new global food and beverage product introductions with whey protein set a new record in 2020, coming in at 7,409 new whey protein products. One of the biggest changes is that consumers are now asking for premium quality whey products. While many dairy plants already have the evaporator and spray drying systems required for whey production, a few tweaks to existing processes might be needed to produce premium quality whey products. Since whey protein isolate (WPI) requires 80% protein content for USDA labeling purposes (as opposed to the 36% protein required for whey protein concentrate (WPC), this may also require an upgraded filtration system and a slight upgrade of the facility’s lab.
Go with the flow
Before making changes to processes, carefully consider the flow of people and products within a dairy processing plant. Start with these questions:
- Will the storage vessel be in the way of a building expansion or block off needed hallways?
- If equipment is rearranged, will drains from raw areas pass through pasteurized areas?
- Will air handling maintain a positive flow of air in the right direction and control humidity where needed?
- Is proper drainage addressed after adding on to a legacy plant?
Plan for expansion
Some dairy processors operate much the way they have for decades—part by part, machine by machine. As dairy processing plants grow and evolve to meet demand, each new process or piece of equipment adds to the intricate puzzle. It might seem the simplest solution is to add square footage. But when planning for an expansion, keep building safety codes in mind—including fire truck access and sprinkler systems. Even a small expansion could trigger major upgrades mandated by city or state laws.
Consider an existing dairy processing plant looking to expand. The short-term plan may be to simply add on to a room, connect all utilities to drain back to the existing space, and add storage vessels outside of the new space. Although this may address immediate needs, it may create unforeseen bottlenecks or problems for the next expansion.
As dairy processing plants undergo expansions, an ill-fitting line can complicate cleaning and create waste. Even a seemingly small renovation or expansion can have ripple effects throughout a facility. For example, locating things far apart calls for longer pipes and bigger pumps—not to mention extra cleaning and wasted product sitting in the pipes.
Avoid headaches and reduce plant costs by carefully planning a staged dairy plant expansion. To do so:
- Map out an expansion plan.
- Configure plant layout, zoning, and segregation.
- Make room for cold storage, product collection, offloading, and ventilation.
- Review building codes.
- Analyze the ergonomics of system/equipment design.
Execute your plan
Unleash process simulation
In general, dairy plants are trying to fit more into a smaller footprint than ever before. Process simulation is a powerful tool that can help facility stakeholders better understand their needs and compare alternative design solutions. Process simulations can be used to evaluate process alternatives for everything from a single unit operation to an entire facility—before risking capital expenditures.
Recently, CRB used process simulation while assisting with a food manufacturer’s expansion. The models were validated for accuracy using historical performance and consultation with the client’s subject matter experts. Using the model, CRB performed a series of studies for the facility feasibility study that evaluated the traffic and materials flow for the following scenarios: centralized palletization, end-of-line palletization, and product reload capacity. Each scenario was characterized in terms of throughput measurement; labor requirements; equipment utilization; people and forklift truck traffic; and staging, space, inventory, work-in-progress. CRB coordinated the study results with the client’s packaging team to address facility and equipment modifications, which were required. As a result of the packaging simulation, it became clear that an entire module could be eliminated from the packaging lines without negatively impacting profits.
Work with an integrated project delivery team
Designing a facility that meets both short-term and long-term needs requires a holistic view. An integrated project delivery (IPD) team can identify, plan, and execute your dairy plant expansion project with an eye on both your short- and long-term goals.
Companies that house architectural, engineering, and construction teams under the same roof, have a head start towards integration because they can offer a comprehensive understanding of facility and equipment design, as well as constructability. CRB’s ONEsolution™ is based on the foundation of IPD, with our own unique approach to driving exceptional results through the principles of lean integration.
The right team for your dairy project can examine plans across building codes, functions, utilities, and hygienic processes. And they can provide a full project solution from initial planning through operational readiness. In short, they can see past today’s needs and plan for tomorrow’s successes.
Looking to grow your dairy processing plant? Get in touch with our team of dairy experts today to plan for tomorrow.