Recycling Technologies: Making Plastics Digestible
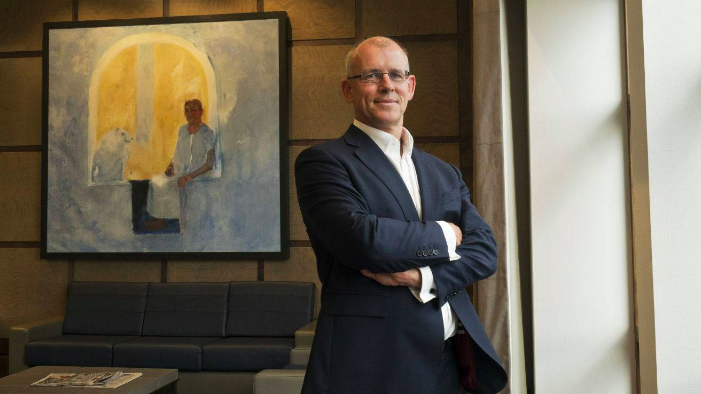
Originally published on Barclays
In 2016, Recycling Technologies was part of the first cohort of the Barclays Unreasonable Impact accelerator, which supports entrepreneurs that are providing solutions to some of the world’s biggest challenges. Two years on it has booked £65m of future sales and is opening a UK factory with capacity for 300 employees. Founder and CEO Adrian Griffiths tells us the story of his company and how it plans to change the world of plastic recycling.
“If you create a technology that means people don’t want to throw plastics away because they can make some money by doing something better with them, then you can change the course of things.”
The idea behind Adrian Griffiths’ company, Recycling Technologies, first came to him in 2010, when he was looking at a Warwick University project on plastic waste. “I was one of those people who would put plastic into the right bin, then a chap would take it away, and I thought it was all done. But when you dig beneath the surface, you realise only 10% of plastic is recycled, and only 2% is recycled back into the product it came from – it dawned on me that there’s an enormous amount of material with which we can do something better. Plastic has a great place in the environment in cutting down on food waste and carbon emissions – just as long as you do something sensible with it at the end of its life.”
In 2016, Griffiths was invited to join the first cohort of Unreasonable Impact – an accelerator partnership between Barclays and Unreasonable Group – and accepted out of “a degree of curiosity common to start-up companies”. While on the programme, he says: “We met a lot of great people. We stay in touch with most of the other nine companies: there’s a collegiate sense still there. And we can tap back into Barclays to some of the people we met.”
Fast-forward to 2018, and Griffiths’ company has booked £65m of sales of their future output, while opening an assembly facility in Swindon, South West England with plans to take on 300 employees.
The technology behind Recycling Technology’s proposition – processing recyclable plastic into oil that can be re-used in plastic production – existed, says Griffiths, a former management consultant, but the economics couldn’t work until his company found a way of “shrinking down the process”:
“Petrochemical companies had been doing this at the end of the 90s, so it wasn’t so much the process that was difficult to conquer, it was how to get it to work economically. They wanted to build big central facilities and transport plastic large distances, but plastic is very lightweight and very low cost – that’s why it’s fantastic packaging material – but when it’s waste it’s still lightweight and zero value, so you don’t want to transport it any distance. So, with high capital cost and high operational cost, they couldn’t make the economics of it work.
“I thought: what if you shrink this thing down and build a machine rather than a refinery? We’ve designed a mass-produced machine that we can take to waste facilities around the world. We sell the machine to the facility operators, who can use it to turn the materials back into oil. You can then sell the oil back to the petrochemical companies, who can make more plastic from it. It makes plastic a circular economy.”
Local Profits
Keeping the profits from the first 12 machines, Recycling Technology plans to expand quickly: “The factory from start-up to full capacity will take 300 employees. It will start making the first fleet of 12 machines and then scale to making around 200 machines a year.” Griffiths is looking forward to bringing this manufacturing capability to Swindon, having recently signed a lease on a 28,000 square foot building: “We’ll be providing a lot of jobs, including apprenticeships from the local college of technology. We’re involved in (the charity) Speakers for Schools, creating awareness for routes into the company.
The high-value manufacturing and the education side and the increase in qualifications for young people should be good for the local area.”
More jobs will be created Europe-wide in operations and service teams looking after the company’s flagship RT7000 machine, fitting in with Unreasonable Impact’s aim to support growth-stage ventures that can rapidly scale to having over 500 employees.
The company, which banks with Barclays in Swindon, has £65m of sales booked against its machines’ future production. “You only need to get a couple of these up and running”, says Griffiths, “and they spit out a lot of cash.” The company’s relationship with the Bank also extends to Canary Wharf, where Barclays’ employees have been advising Griffiths on Recycling Technology’s brand and marketing.
Griffiths’ aim is to have the capacity to make seven million tonnes of oil from 10 million tonnes of plastic by 2027, which is, he says, “not very much when you consider we currently use about 320 million tonnes of plastic in the world, and 90% of it is buried or burnt or lost. But the current capacity for plastic recycling in the UK is 360,000 tonnes, so 10 million looks a big number compared to that – and it’s more than twice what the UK uses in a year. Europe’s plastic recycling capacity is three million tonnes a year: we could quadruple the recycling capacity of Europe within 10 years.”
Global Impact
Further opportunities for growth and impact could come in Asia: “We’ll be providing income for people to bring plastic to the machines rather than dumping them in the rivers. So, we’ll hopefully start to make a big difference out there as well.”
The situation in Asia also shows just how much plastic pollution is an interlinked global problem, says Griffiths. “In the UK we have 360,000 tonnes of recycling capacity but we recycle 1m tonnes – so where’s the difference between those figures? The difference is that we stick it on a boat and ship it to Vietnam or Sri Lanka or Bangladesh. The stuff going into the ocean there is not necessarily their plastic – it’s what we’ve sent them. Europe ships more recycling than it deals with itself, but we’re shipping to countries without waste infrastructure. What we call ‘recycling’ is actually the stuff that’s ending up in the Mekong River. It stops UK recyclers having to pay for landfill for non-recyclables – but when they’re shipped to the Far East, they’re still non-recyclables – it’s just they can get rid of them at lower costs than we can in this country. It drives you mad.”
So, was the idea to build a business or to make the world a better place? “You can’t do one without the other,” replies Griffiths. “You’re not going to save the planet by hugging a tree. If you want to change things you have to do it by creating a business, and that business then has to make money. If you can actually make something that’s going to do a lot of good in the world – but it makes some money – then the chance is it’ll succeed.”